Komplexes Handlingssystem zur Beschichtung von Rohrmuffen
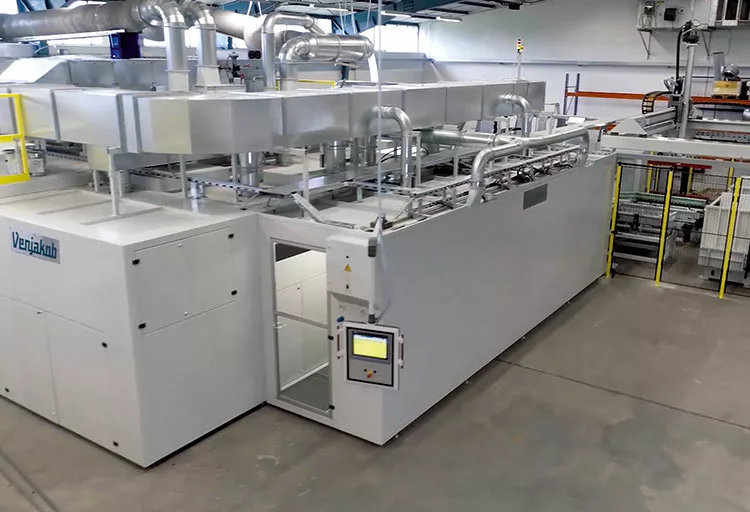
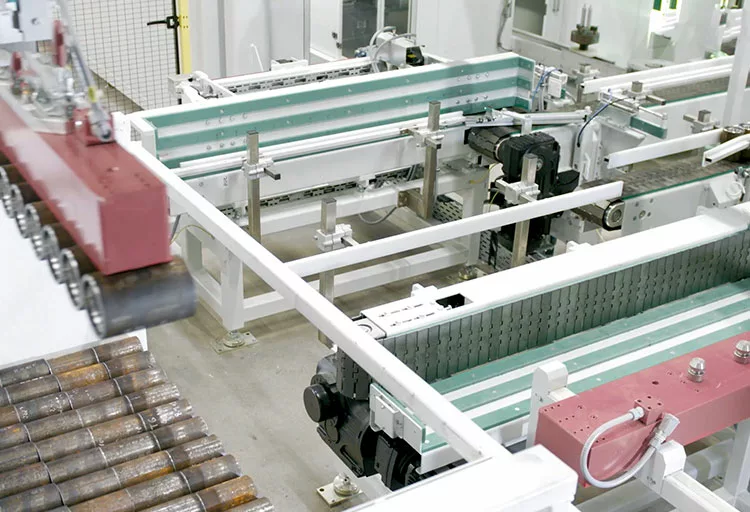
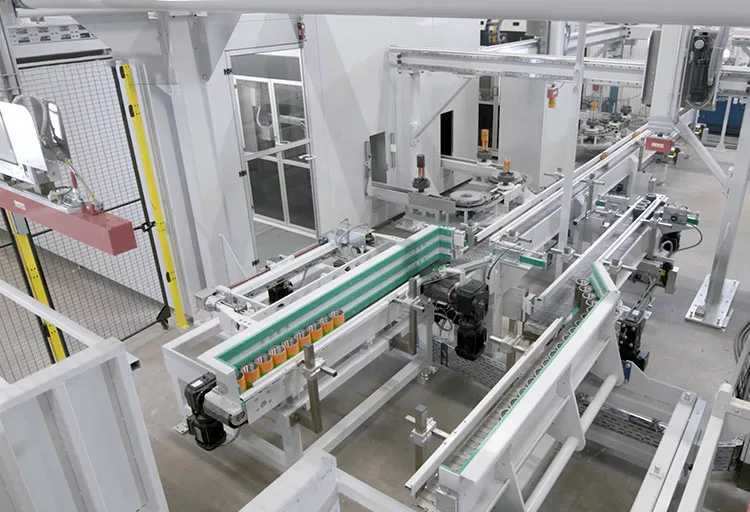
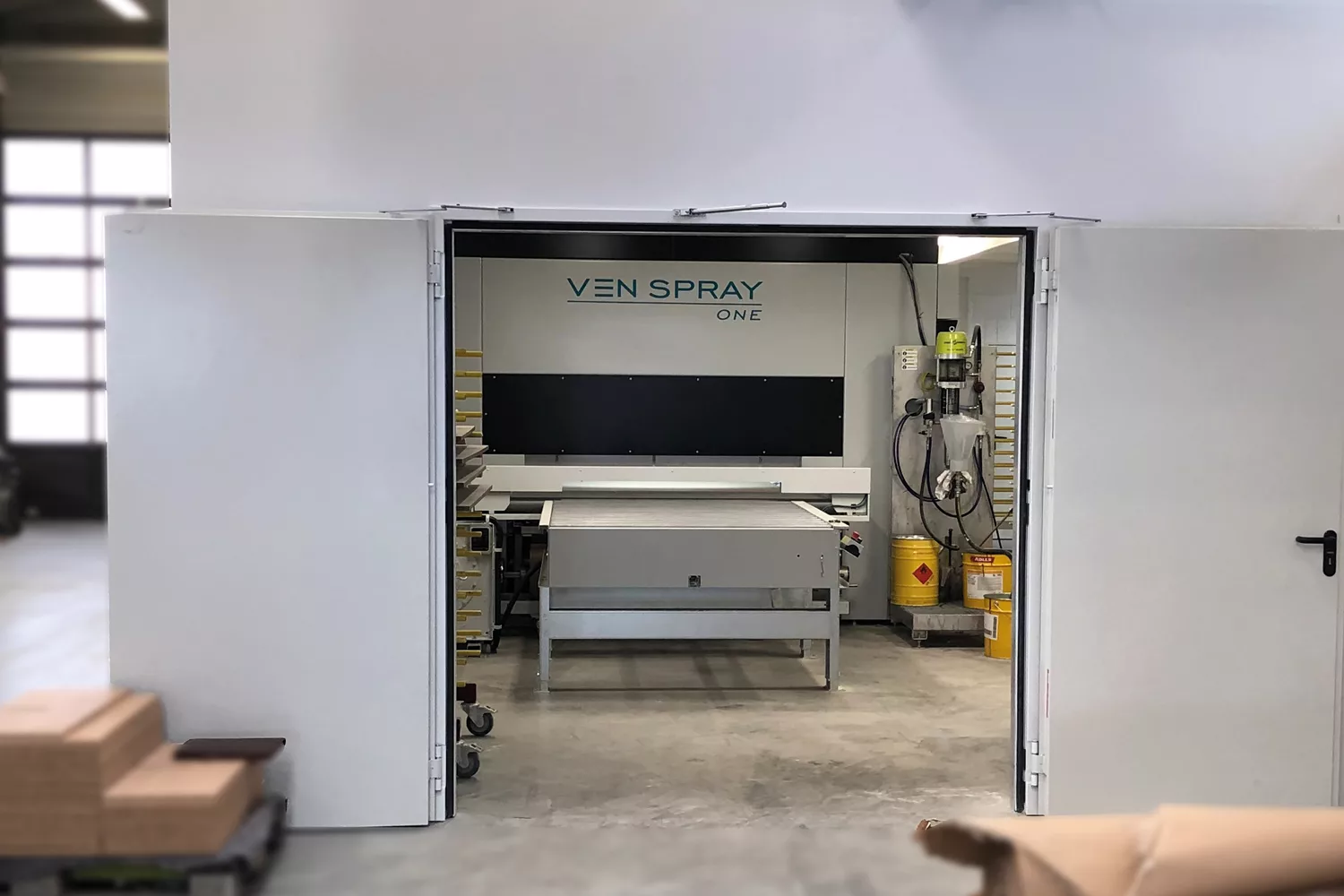
Das russische Unternehmen OMK Vyksa produziert verschiedenste Rohre, z. B. für den Bau von Öl-, Gas- und Wasserleitungen. Gigantische Pipelineprojekte in über 20 Ländern weltweit werden mit den Rohren von OMK Vyksa ausgestattet. Das Unternehmen wollte die bisher zugekauften Rohrmuffen im eigenen Werk selbst herstellen. Damit sollte nicht nur der eigene Bedarf gedeckt, sondern die gesamte Produktpalette aus einer Hand angeboten werden.
Kurze Wege für höchste Effizienz
Für dieses Vorhaben wurde eine neue Fertigungshalle gebaut, in der eine moderne Fertigungsstraße zur Herstellung von Rohrmuffen unterschiedlicher Größe implementiert wurde. Auf einer Fläche von 15,8 x 29 Meter fügen sich zwei vollautomatische Beschichtungslinien von Venjakob, zum Lackieren, Signieren und Markieren von Rohrmuffen, nahtlos ein. Diese decken die gesamte Spannbreite der unterschiedlichen Rohrmuffengrößen ab. „Bei der Projektierung der neuen Anlagentechnik war es für uns wichtig, dass alle Herstellungsprozesse in einer Halle stattfinden. Kurze Wege für höchste Effizienz. Die Ingenieure von Venjakob erfüllten mit diesem kompakten System dieses wichtige Kriterium“, sagt Dimitriev Alexander Michailowitsch, Projektleiter OMK Vyksa.
Automatisierte Beschichtung im Sekundentakt
Eine Anlagenlösung nach Maß, bei der sich Venjakob nicht nur als Spezialist für Verfahren in der Oberflächenbeschichtung zeigt, sondern ebenso kompetent und erfahren in der Planung, der Entwicklung und der Umsetzung vollautomatisierter Förder- und Handlingskonzepte für ein Höchstmaß an Wirtschaftlichkeit. Der gesamte Beschichtungsprozess – von der Bestückung an der Verladestation über die einzelnen Bearbeitungsstationen hinweg bis zur Entnahme – findet ohne Eingriff von außen statt. Die Anlage ist auf eine große Spannbreite an Rohrmuffentypen ausgelegt, die sowohl von außen als auch von innen beschichtet werden können. Die komplette Bearbeitungszeit ist abhängig von den Abmessungen der Rohrmuffe und dauert zwischen 16 und maximal 60 Sekunden.
„Bei der Projektierung der neuen Anlagentechnik war es für uns wichtig, dass alle Herstellungsprozesse in einer Halle integriert werden. Kurze Wege für höchste Effizienz. Die Ingenieure von Venjakob erfüllten mit diesem kompakten System dieses wichtige Kriterium“
Dimitriev Alexander Michailowitsch
Transportsystem passt sich automatisch an
Eine besondere Herausforderung lag in der Variabilität der Rohrmuffen-Typen. Das bedurfte einer gewissen Anlagen-Flexibilität sowohl beim Beschichtungsverfahren als auch im Handlingssystem. „Das vollautomatisierte Handling musste auf mindestens 20 verschiedene Durchmesser von Rohrmuffen ausgelegt sein bzw. sich auf jeden dieser Durchmesser leicht umrüsten lassen“, berichtet Kornelius Berg, Vertriebsingenieur von Venjakob Maschinenbau. Diese Anforderung konnte über die Steuerung gelöst werden. Der Maschinenbediener wählt über ein Programm den entsprechenden Durchmesser der Muffe aus. Nach der Auswahl stellt sich das gesamte Transportsystem automatisch auf die Muffengröße ein. Lediglich die Werkstückträger für die Innen- und Außenbeschichtung sowie die Greifsysteme für die Bestückung und die Entnahme werden manuell umgerüstet. „Diese wurden so konzipiert, dass sie stufenlos einstellbar sind. Ein Austausch von Zentrieraufsätzen oder -scheiben ist nicht erforderlich. Das ist ein großer Zeitvorteil“, hebt Kornelius Berg hervor.
Be- und Entladen im Flow
Eine zweite wichtige Anforderung für die Projektierung der Gesamtanlage hatte mit den Kapazitäten der Aufstellfläche zu tun. Für den optimalen Prozessablauf ist es notwendig, dass der Mitarbeiter, der die Muffen-Container mit dem Stapler zur Beladung anliefert, an der gleichen Stelle die fertig beschichteten Muffen wieder aufnehmen kann. Dafür wurden das Belade- und Entnahmeportal nebeneinander angeordnet. Die zu beschichtenden Muffen werden über eine Wendestation dem Transportsystem für den Einlauf zugeführt und die fertigen Muffen über eine weitere Wendestation dem Transportsystem für den Auslauf, das auf der gegenüberliegenden Seite zum Entnahmeportal führt. So ist eine kontinuierliche Be- und Entladung möglich.
Der Prozess
Verladung und Platzierung auf Werkstückträger
Im ersten Schritt werden die Rohrmuffen automatisch in einem Container in mehreren Lagen übereinander angeordnet. Aus dem Container werden die Muffen reihenweise entnommen, auf der Wendestation platziert und dann senkrecht gestellt. Die Be- oder Entladung kann mittels Magnet- oder Gabelgreifer erfolgen. Der Weitertransport zum Beladeportal geschieht über ein Kettentransportsystem. Von hier aus werden die Rohrmuffen einzeln auf die Werkstückträger platziert. Diese können stufenlos auf die gewünschte Größe der Rohrmuffen eingestellt werden – die Spindelaufnahmen stehen dabei enger oder weiter zusammen.
Lackier-, Markier- und Signierprozess im geschlossenen System
Die Vorwärmung, die Außen- und Innenbeschichtung sowie die Warmlufttrocknung finden in geschlossenen Systemen auf einem Spindelkettenförderer statt. Zwischen den einzelnen Beschichtungsvorgängen fahren die Muffen über eine Trocknungsstrecke.
Innengewinde wird vor Korrosion geschützt
Nachdem die Außenbeschichtung abgeschlossen ist, werden die Rohrmuffen auf die Werkstückträger für die Innenbeschichtung übergesetzt. Hierbei werden die Muffen auf einen weiteren Spindelkettenförderer für die Innenbeschichtung platziert. Ebenfalls im geschlossenen System wird die Gewindekonservierung mit einer Öl-Wasser-Emulsion durchgeführt.
Entnahme- und Beladung direkt nebeneinander
Nach der anschließenden Warmlufttrocknung werden die fertigen Rohrmuffen auf das Auslauftransportband abgesetzt und der Wendestation für die Sammlung zugeführt. Im letzten Schritt werden die gewendeten Muffen reihenweise über den Magnetgreifer in mehreren Lagen in den Entnahmebehälter abgesetzt.
Besonderheiten der Gesamtanlage
- Vollautomatisiertes Handling
- Flexible Auslegung auf verschiedene Rohrmuffen-Typen
- Automatische Umrüstung des Transportsystems
- Stufenlos einstellbare Umrüstung von Werkstückträger und Greifsystem
- Belade- und Entnahmeportal nebeneinander
- Alle wichtigen Anlagenpositionen sind gut zugänglich
- Wartungsarmes System
- Nahtlose Integration in den gesamten Herstellungsprozess
- Kompakte, modulare Bauweise
Ihre Ansprechpartnerin
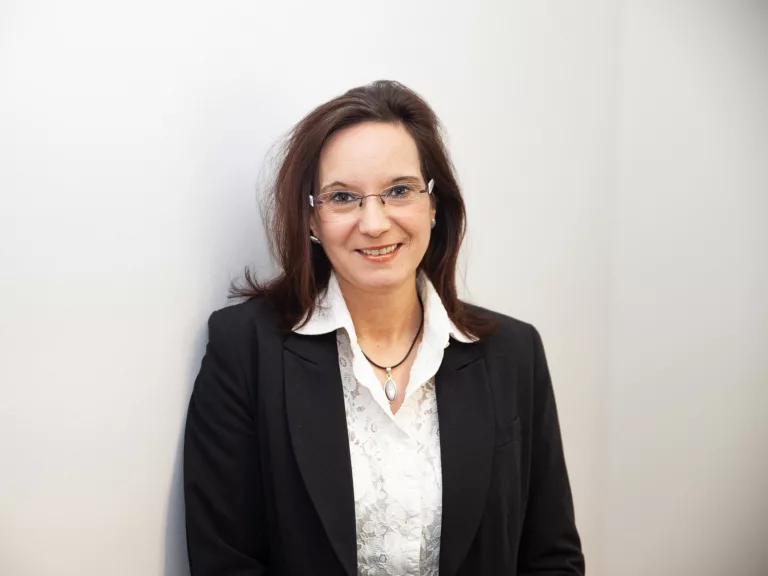