- Venjakob
- Surface treatment
Surface treatment with Venjakob
Solutions for a practically infinite range of surface treatments
For us, a typical work assignment might be something like: "Make that blue." And “that” can be just about anything. A cup. A piece of furniture. A dashboard in your favorite vehicle. Some object in the spaceship you're taking to the moon next week. “That” can be made of metal, of steel, of wood, of plastic, of basically any material you can imagine. And that which ultimately makes it blue or red or green is a specific paint that consists of specific components that are particularly suitable for a specific surface. Sounds almost a little confusing when you read it, doesn’t it? But these are just some of the factors that we at Venjakob deal with day in, day out when we develop tailor-made system concepts for our customers. Surface treatment is right at the top of our list of keywords. After all, it's never just about the coating. It’s always about perfectly coordinating all factors so that the object you would like us to turn blue first of all becomes blue and secondly stays blue. And not just once, but countless times. Always in the same impeccable quality. Our task is, time and time again, to find a solution for these practically uncountable types of surface treatment. Read more to find out how we do that.
Metal, steel, plastic, wood and glass etc. each require their own special surface technology
As a general rule, if you want to coat a surface, you first have to clean it. Specifically, this means selecting suitable surface technology for the workpiece, the material, the nature of the surface and the quality and function of the coating. This could be a specific cleaning process, for example dry ice cleaning, or degreasing or dust removal. It could be, but it doesn't have to be. While metal and steel usually need to be degreased before coating, wood more often undergoes abrasive processes, such as sanding. And you can even combine multiple methods: For example, we can equip a dust removal unit with additional brushes if required. To put it simply: Technologies, methods and materials can vary from one surface treatment to the next. It depends entirely on the industry. What is essential to one customer is merely a nice add-on for another. Some need the full range, others think they can do without any of it. And quite a few who believed the latter ended up approaching us for a retrofit later on. It goes without saying that retrofitting is part of our services, but the earlier we are involved in a project, the less retrofitting is required later. As a rule, none at all.
Different types of surface treatment
At Venjakob, we differentiate between pretreatments like
- cleaning processes using dry ice blasting, ionization and dust removal, degreasing or aqueous, alkaline neutral cleaning agents
- processes for activation by flame treatment, plasma or flame silicification.
- abrasive processes using brushing, sanding, smoothing or blasting.
Actual surface treatment includes the various coats and finishes or even application of adhesive. So applications like
- spraying with 1-component, 2-component, water-soluble or UV-curing coatings,
- flow coating for waterproofing, glazes or primers,
- dip coating of metal or steel parts,
- roller coating and curtain coating.
At the end, the workpieces are dried. More than one technology is available for this step, too. For example, drying with
- infrared dryers for gentle drying of dispersions, water-based and solvent-based coatings,
- UV lamps for UV-curing coatings or adhesives.
What does surface treatment get you?
Reliability. As a rule, each coating serves a specific function, for example protecting the surface. Coatings applied to metal often protect it from corrosion. Another purpose is the visual effect, the aesthetic appearance. Sometimes – for example with a glaze – the coating also serves as decoration. Properties such as conductivity, wettability, friction and insulation also play a role – depending on the materials involved and the intended use of the products. Coatings and surface treatments vary from application to application, from industry to industry and from market to market. And of course from company to company. What one customer considers the best solution is completely unthinkable for another. But not for us. At Venjakob, nothing is unthinkable. This is precisely the reason why we can offer our customers the best possible process for them: Because sometimes we open up a completely new space of ideas for them. And speaking of space, that brings us to a topic that, on the face of it, has nothing to do with surface treatment. But actually it does: the matter of space!
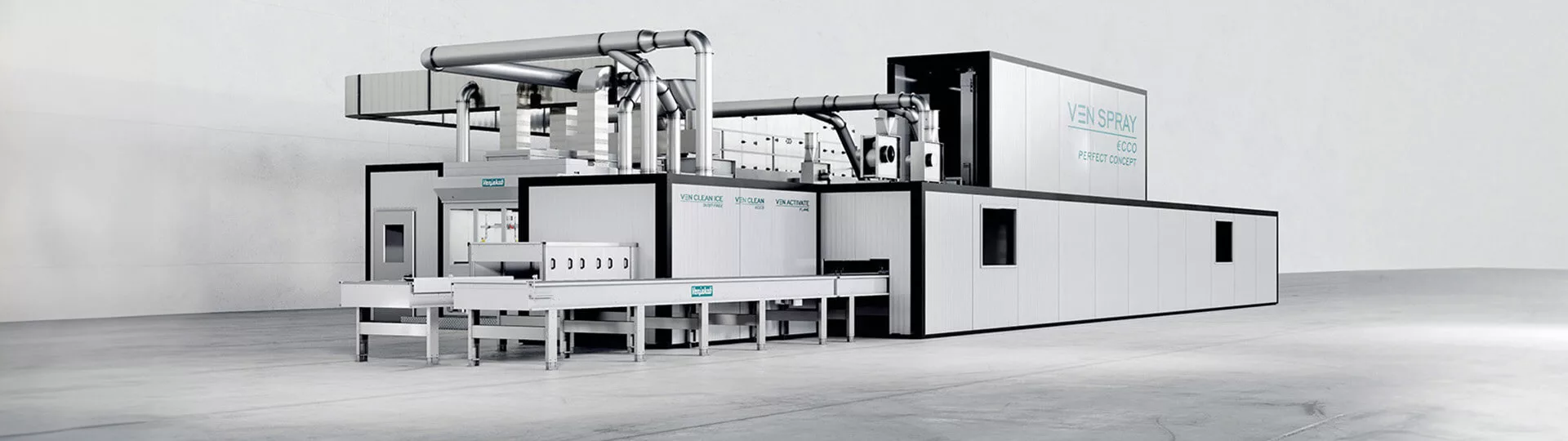
Leaving and creating space for the best possible surface treatment
If you have followed us this far, you will have noticed that there is no such thing as the one single coating system. The same applies to processes. There is no one single process. Each process has to be developed based on the specific task, the specific requirement profile. And often it even has to be adapted to the available space. For instance, a company may already have a coating system and now needs a new cleaning system or an upgrade of the existing system. A drying system, for example. Sometimes there is just not enough space for that. There isn’t always a convenient piece of land on which to build the best of all possible coating worlds. But we are prepared for these cases. We don’t claim that anything is possible. But we make many things possible. That’s because we know what companies need, because we understand how they think, because in almost sixty years in the business we have gained unique experience in solving the kind of problems that arise all the time.
So last but not least: Let's talk - about surface treatment
Surface treatment is a complex field that ensures the quality of products in countless applications in manufacturing and production in almost every industry. The materials, methods and technologies of all potential coatings need to be perfectly adapted to each other and combined in a single process. A process as complex as that can only succeed with a partner who has the necessary experience to plan, design and implement it. Trust is a crucial factor. But as they say: Trust but verify! That is exactly why we at Venjakob have our technical center. That is where we test all the components of the systems we design for our customers, but not just that! We also offer our customers the opportunity to come and see for themselves on site that all the systems they will later use in industrial production are working perfectly. Incidentally, we don’t just maintain the one technical center at our headquarters in Rheda-Wiedenbrück. Our US subsidiary Nutro also runs one. Our technical centers have met with a great response on both sides of the ocean. Just come visit us and see for yourself. Perhaps we can also take this opportunity to talk about surface treatment.
Your contact
Contact us now for a personal consultation regarding your spray booth!
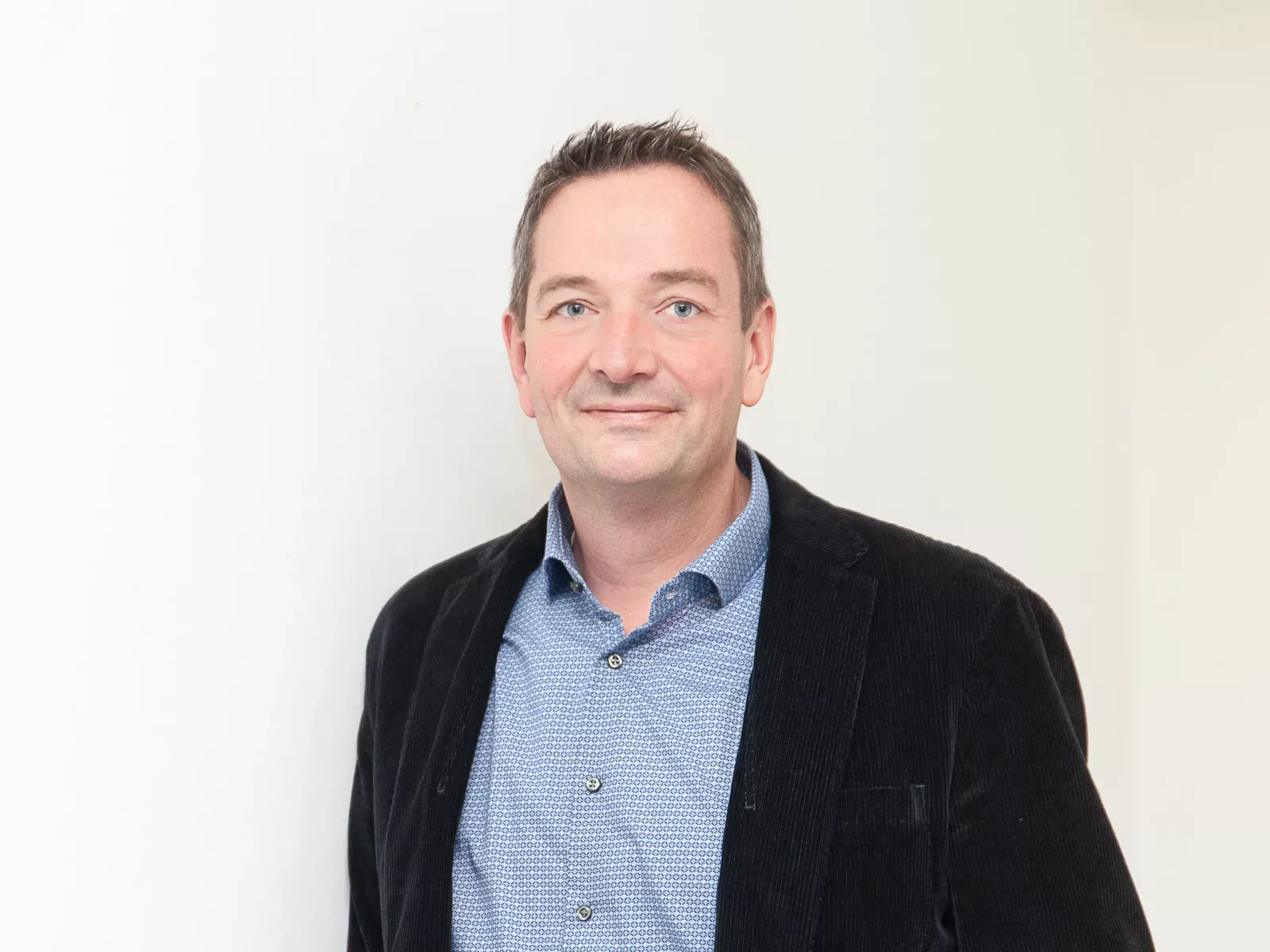
Gert Grosse Deters
General Industry|Automotive
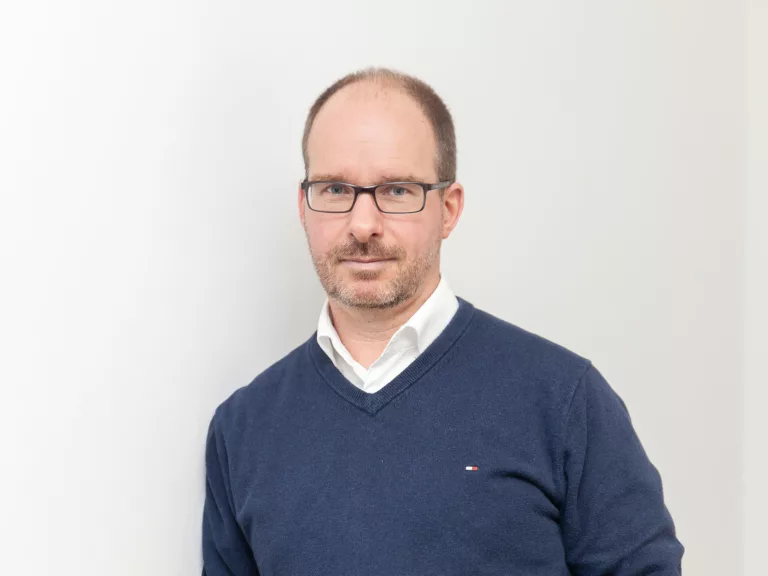
Christian Streit
Wood|Building Materials