- Venjakob
- Finishing | Coating
- Spray coating
Spray coating with a Venjakob coating system
Usually, one of the first questions our customers ask us when they visit us at our site in Rheda-Wiedenbrück is: How does a coating system actually work? Well, if there was a way to answer that question briefly, this page would not be nearly as long as it is. So, we’ll sum it up to give you a better idea. Let’s start by giving you an overview of the process itself: How does a spray booth work, when is a spray gun used? And can you automate the whole process? Usually, yes. Then we’ll give you a tour of all the different applications – from wood and glass through metal and plastics to automotive and aerospace. Last but not least, we’ll provide some more detail. If that’s exactly the information you’re looking for, simply scroll down. And one more thing: This is just a website – it can’t give you more than a glimpse. If you really want to learn how to apply coatings and finishes properly, simply contact us! We love to help – and we have incomparable expertise when it comes to spray coating.
Each Venjakob coating system and spray booth is made to order
A spray coating system/spray booth applies a wide variety of liquid materials to a surface using a spray gun or rotary atomizer. Unlike roller application, spray coating also permits finishing of three-dimensional workpieces. If the workpieces you wish to coat have a rough surface or hollow spaces, you can also use dip coating as an alternative method. Spray coating guns can either be installed in a stationary position or moved via linear axes or robots. We will be happy to help you find the ideal solution for your requirement profile.
Wet coating systems using the spray coating process for lacquers, adhesives, adhesion promoters and functional layers
Sprayed fluids – coating material
- 1-component coating
- 2-component coating
- Water-based coatings
- Solvent-based coatings
- UV coatings
- Coating material combinations
Other sprayed fluids
- Stain
- Nanocoating
- Anti-scratch coating
- Sol gel
- Adhesive application
Spray gun variants
- Air
- Airmix
- Airless
- Electrostatic
Saving resources through professional spray coating
When planning your coating systems or lines, we attach great importance to the conservation of resources. This starts in our own production facilities and ends with an optimized system for spray coating at our customers’ plant. We will make sure you, too, can save energy and coating material.
Our minimum material quantity supply, the “paint shuttle”, is perfect for you if you are working with small coating volumes. If you have to change colors frequently, the fully automatic quick color change system has great advantages: In addition to saving resources, this process also saves you time. Moreover, we can integrate material recovery systems in your spray booth on request, and you can also acquire a suitable exhaust air purification system from Venjakob Umwelttechnik.
Applications for Venjakob coating systems and spray booths
From a spraying station to the spray booths, each Venjakob coating system is a unique piece with a modular design. After all, the applications of our coating systems cover the entire range from A for automotive to Z for zinc. To put it simply: Each category, each field of application, has countless distinctions of materials such as glass, metal, wood or plastic. There are numerous variants of everything and each of them requires its own special coating method. This does not always have to be spray coating. Dip coating, flow coating or roller coating are likewise available options. But no matter which you choose, we can promise one thing: At the end, the coating – or the adhesive, or the stain – is where it needs to be. Whatever you’re applying, you will be satisfied.
Building materials – this includes facade cladding, acoustic ceilings, insulating materials and insulating materials such as glass wool, rock wool or wood wool. Building materials include stones such as paving stones or patio slabs, as well as corrugated sheets, roof tiles and concrete. Building materials are needed like sand on the sea – in other words, it is always a matter of high material throughput and many color changes. Our coating systems for building materials are designed for this. And because many color changes also affect paint consumption, we at Venjakob always keep an eye on paint recovery.
Everything that connects building materials with our coating systems can be found here.
Glass is a very special material. It can be used in many different ways. And the coating requirements are just as varied. At Venjakob, we offer customized coating systems for spray coating decorative glass or functional glass. Functional glass requires either hydrophobic or hydrophilic coatings. We offer solutions for both. We also offer solutions for façade and window glass – so-called architectural glass, which has to withstand strong climatic and weathering fluctuations. Even more challenging are the requirements for coatings for safety glass, which must be heat-resistant, break-proof or even bullet-proof. Our coating systems contribute to all of these tasks. For example, with reflection-reducing sol-gel applications or self-cleaning coatings and coatings with a lotus effect – to name just a few.
Take a look at our coating systems for glass.
Window parts, stairs or staircase elements, interior and exterior doors or even sectional doors such as garage doors or hall doors open up a wide field for spray painting and spray coating. And therefore for Venjakob. We specialize in this area. For example, when it comes to the excellent painting of individual window parts. It’s worth taking a look at our references – whether it’s the flexible edge spray coating system for precise and environmentally friendly door edge coating, the door coating system designed for speed and variability or the fully automatic individual window coating system. The automatic stair coating system is also impressive, as is the resource-saving door painting system. Like all our success stories, these project reports will give you an insight into how we at Venjakob approach orders – objectively, purposefully, customized. But it is only through personal contact that you will get to know the essential, decisive element of our success: passion. This really does flow into every one of our projects.
You’ve already guessed it: you can rely on our paint booths for construction elements.
These are screws, wheels and housings, forged parts, large sheets or plates as well as pipes and sectional steel. Sometimes it’s a coating for pipe sleeves, sometimes intricate small parts for watches. It is always about quality – about a solution that meets the requirements for sometimes very challenging tasks. Surfaces or continuous profiles require different handling than workpieces with complex 3D geometries. Sheet metal needs to be coated differently to steel. All these factors need to be taken into account. And we do. Because we master the entire spectrum of metallic functional and decorative coatings. Because at the end of the coating process, many metallic products not only have to be protected by the coating – for example against corrosion – but also have to look good. We make sure that both is the case.
It’s not just your eyes that shine: our coating systems in use for metal.
Sometimes spray coating is used in kitchens, living rooms and offices are unthinkable without furniture, tables, chairs and fittings that do not contain wood. It is impossible to imagine shopfitting and interior design without coated wood. Even yachts, yacht interiors, contain wood, lots of wood – and here in particular the quality must be impeccable. Wood and furniture can include many things – real wood surfaces, for example. Or laminated surfaces, filled and textured. From raw wood to panel construction, the specific, material-related characteristics of these surfaces must be taken into account. And this does not even include the multitude of shapes that can be coated with a wide variety of lacquers, stains and adhesives. Sometimes spray coating is not enough. In this case, we recommend processes such as dipping, flooding or rolling.
To sit in and put your feet up: All about our solutions for wood | furniture.
Automotive is an industry in itself. Basically, all applications come together here – perhaps with the exception of components. But apart from that, almost every form of coating is represented: Car windows with glass coatings, housings, body components and chassis parts with metal coatings, seals as well as interior and exterior parts with plastic coatings – and last but not least, there are interiors finished with wood coatings in luxury limousines or even in campers or caravans. Commercial vehicles also fall into these categories. Even brake disks, wheels and hubcaps are coated. In short: everything comes together here. And if any proof of quality is required: Nowhere else is looked at so closely – by millions of quality inspectors who have their own paint object in the garage. We’re a little proud of that too.
The things we paint in the automotive sector are pretty crazy.
Spray coating systems for functional coatings, decorative coatings or effect coatings? Didn’t we already have this with glass? Yes, we have. But what sounds similar can be subject to completely different requirements. Plastic coating often involves protection from the sun and UV rays. Or protection against moisture and cold. To improve scratch and abrasion resistance. Decorative coating by spray painting enables very different effects – such as day & night design, metallic effects or high-gloss piano effects. Also possible: coatings that imitate electroplated finishes. Sounds pretty extravagant, doesn’t it? And it is. Finally, there is something else: effect coatings that convey haptic sensations – for example leather soft touch. Not everyone can do that either. You can – with our process experience.
Find out more about our spray painting booths and spray painting systems for plastic here.
There is one more field of application: aerospace. Everyone knows that quality is the ultimate in everything that takes off. No compromises are made here – and none are tolerated. And to prevent this from happening in the first place, we take a very close look ourselves before our system is delivered to the customer. And because we value all our customers equally – which is precisely why we develop individual solutions for them – we take a very close look everywhere. What we have in our portfolio especially for the aerospace industry: Complete processes for your workpiece – from pre-treatment to production and finishing. Regardless of whether it’s interior parts made of plastic, for example, or structural or connecting elements made of aluminum, etc.
Just take a look at what we have to offer aerospace.
The plant technology at a glance
So what does the process itself look like? What about the details? What about color changes? What about coating material recovery, mist separation and exhaust air purification? We’ve got it. We know what to do. And we adapt to your needs.
Tailored combinations of plant technology for spray coating to help you achieve success
The modular design of our systems makes it possible to create customer-specific solutions. Systems for surface pretreatment and drying, added as needed, create perfect surface quality and permit rapid further processing after the coating process. They are always individually adapted to the coating material used and the workpiece being coated. Unlike other manufacturers, Venjakob offers a broad portfolio of different coating and finishing systems.
- Linear spray coating systems for continuous coating or batch processing: Surface or flat bed spraying system, automatic spraying machines with skid conveyors or power-free systems
- Rotationally symmetrical systems: Coating machines for rotating workpieces in the form of rotary index tables, spindle chain machines (chain-on-edge conveyors)
- Vertical systems
- Coating robots
- Coating systems for moldings and profiles
- Pipe coating plants (interior and exterior)
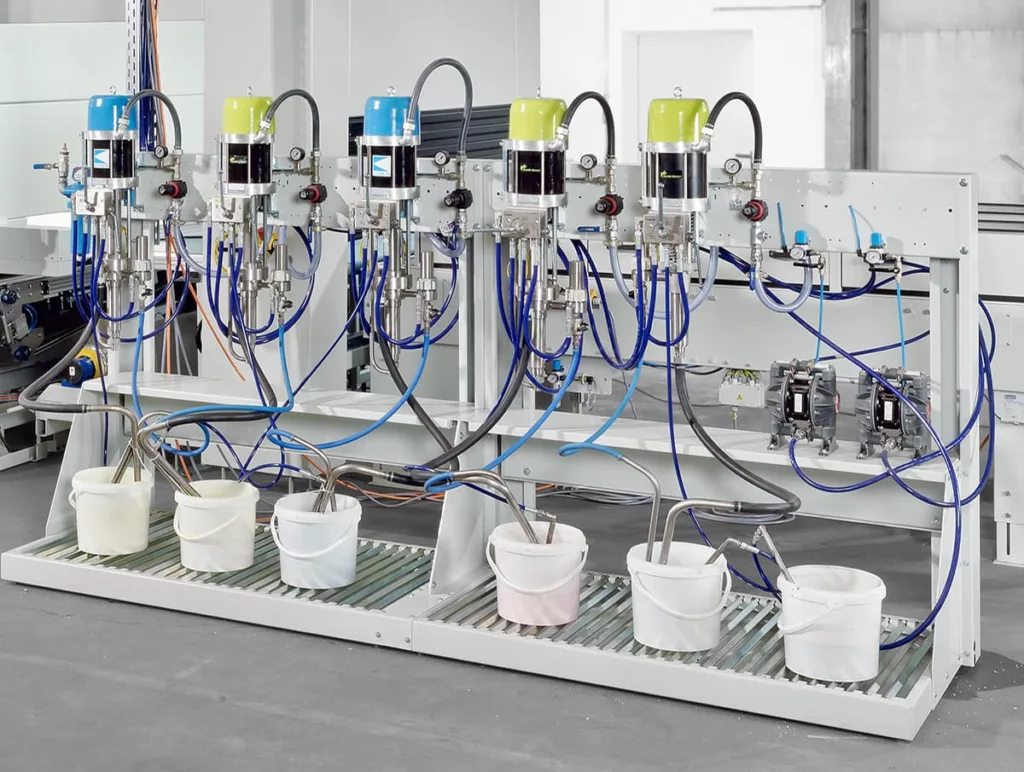
COLOR CHANGE - FLEXIBLE AND FAST
If you have to change colors frequently, Venjakob’s fully automatic quick color change system has great advantages. Aside from saving resources, you save mainly one thing: Time - a lot of time. Our quick color change systems will drastically reduce the time required for color changes in your production. And if you only want to coat small quantities, you can take advantage of our minimum material quantity supply, the “paint shuttle”. These are both highly efficient solutions for companies in any industry that wants to focus on coating, not on changing colors.
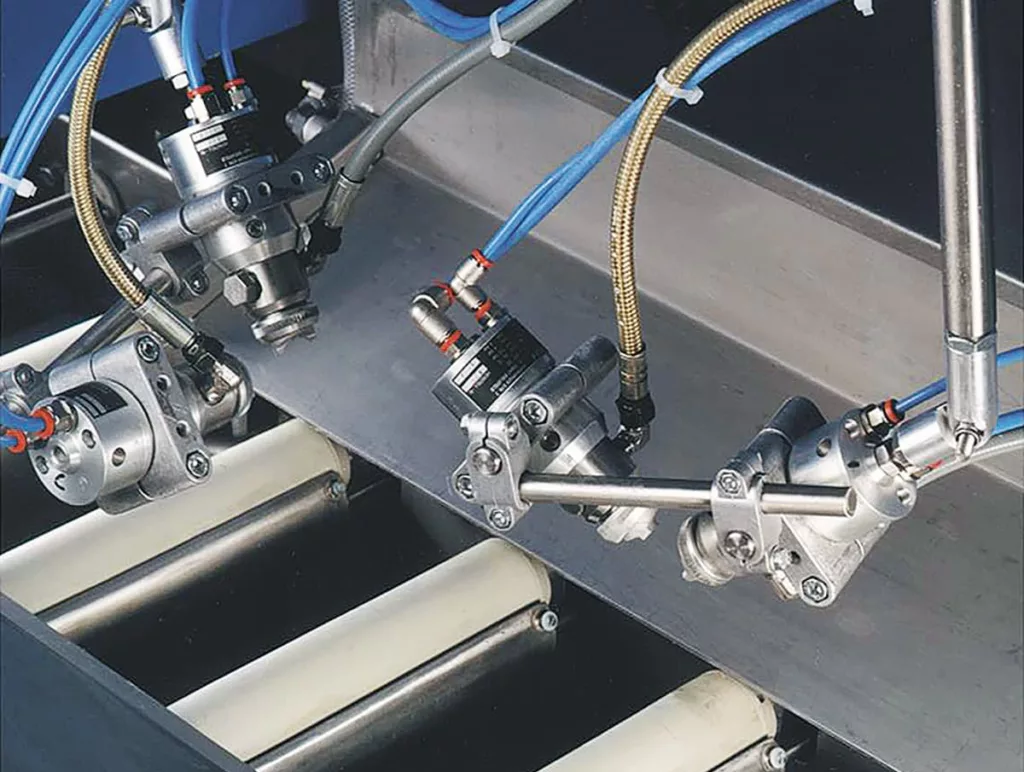
COATING MATERIAL RECOVERY
Coating materials are valuable. However, every coating process involves some loss of material - even just through covering the edges. But not with us. Not for you. Depending on the spray material used, we can provide you with material recovery systems that are cost-effective, environmentally friendly and practical. For this purpose, Venjakob offers mechanical recovery systems as well as systems based on Coolac® technology. Moreover, double-drum recovery units are available, particularly for pipe coating. Material recovery is a smart move that saves you money and benefits the environment.
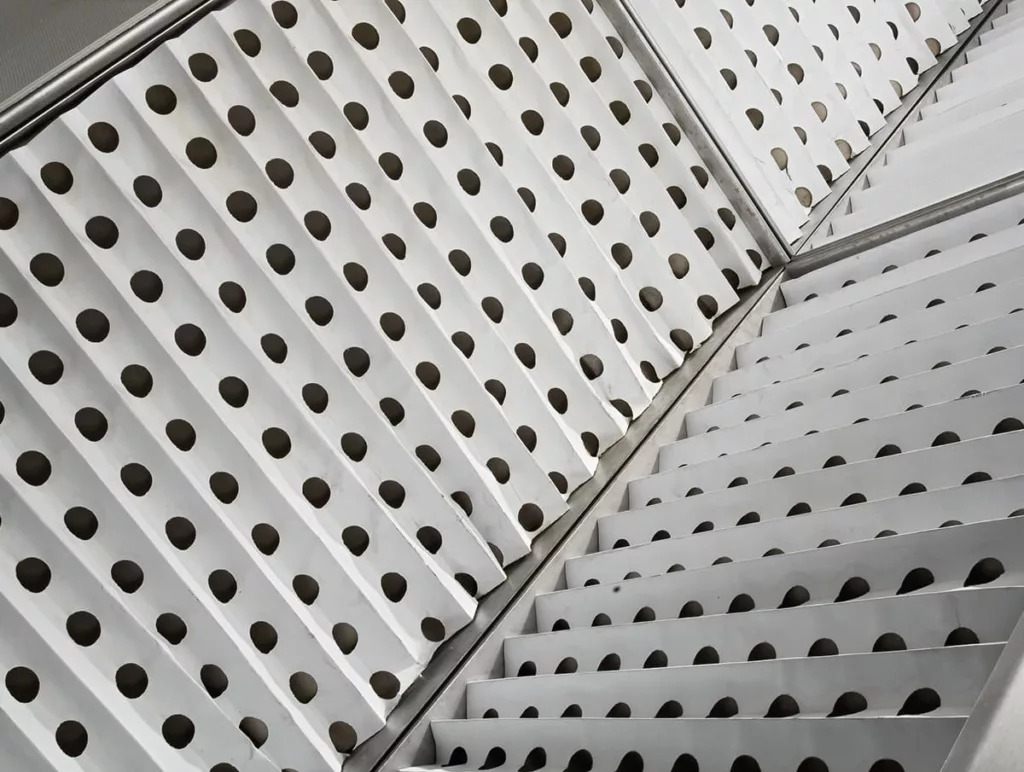
COATING MIST SEPARATION
Our approach is just as tailored when selecting the best system for coating mist separation. Environmental technology and quality are of utmost importance at Venjakob. Therefore, we offer various solutions for the separation and recovery of overspray (coating mist) generated during coating. These are integrated into our spray booths and ensure perfect air management during coating, leading to excellent surface results.
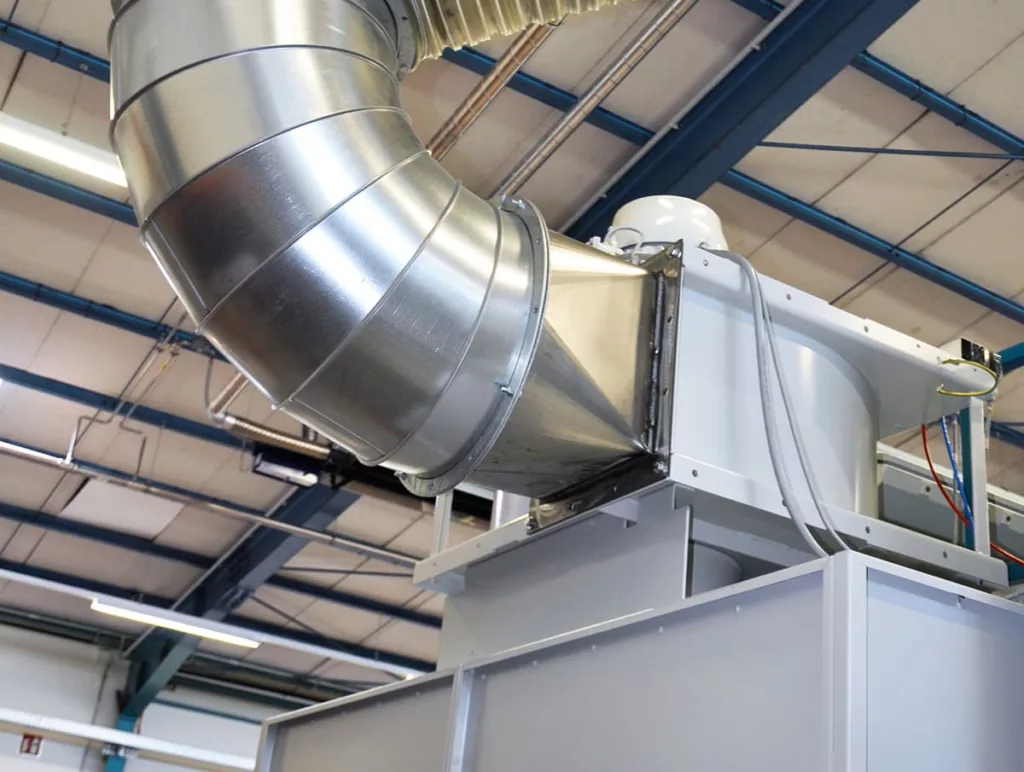
SUPPLY AND EXHAUST AIR SYSTEMS
To optimize the air flow in a coating system, it makes sense for the supply and exhaust air with compressed air to follow the spray and coating jet. For this purpose, all our systems have optimized ventilation and venting systems. Extraction and exhaust air purification in your company is of special importance to us. Not least to protect the environment.
Long-term investment security through Venjakob
As a high-performance partner for a wide range of industries, we implement solutions for your specific requirements. The Venjakob modular system allows existing system technology to be flexibly adapted to new conditions and requirements at a later date. You benefit from long-term planning and investment security.
Contact us now for a personal consultation regarding your spray booth! Because spray-coating with a Venjakob coating system promises a strong finish for your production. We manufacture each machine ourselves to the greatest extent possible in our in-house machine shop. We consider an extremely high vertical range of manufacture essential so that we can react quickly when necessary. This production philosophy is particularly vital so that we can offer you not just a coating system or spray booths, but a complete process from workpiece feeding via automated conveyor technology and pretreatment systems (cleaning, activation or abrasion) to coating and finishing and beyond. That’s because we believe that surface technology includes dryers, drying systems and technology: Drying technology. What you get is not just one machine, but multiple machines. Machines that are perfectly adapted to each other. No matter what perspective you take, your production line will benefit from our experience.
So what’s next? How about you give us a call!
Have you learned how spray coating works? How to coat – for instance, metal – with a spray gun? Do you actually need to know? Probably not! The only thing that matters is that you know that we know. And: Do you now have to order your entire coating line from us? From feeding to stacking? With pretreatment and drying? Do you need to modernize your entire production? And what would that mean for your spray painter’s job? Well, if that’s really what it comes down to, let’s put it this way: Your spray painter will have a much more fun job in the future! Provided they’re the type of person to have fun at their job, of course. After all, there’s always need for spray coating – and your qualified staff can only benefit. Our methods allow them to learn and acquire additional qualifications in the process – and rapidly, too, because our machines are not designed for long training periods. What it comes down to is this: we understand your craft, your industry, and the engineering of machines that can coat the number of products you want to deliver – item by item. Where can you find us? Here in Germany in Rheda-Wiedenbrück. And in the USA, our company Nutro Inc. is there to support you. The solution we give you doesn’t come from a warehouse – it comes from the minds of our development engineers. So contact one of us to get your own customized solution!
Contact us now for a personal consultation regarding your spray booth! Because spray-coating with a Venjakob coating system promises a strong finish for your production. We manufacture each machine ourselves to the greatest extent possible in our in-house machine shop. We consider an extremely high vertical range of manufacture essential so that we can react quickly when necessary. This production philosophy is particularly vital so that we can offer you not just a coating system or spray booths, but a complete process from workpiece feeding via automated conveyor technology and pretreatment systems (cleaning, activation or abrasion) to coating and finishing and beyond. That’s because we believe that surface technology includes dryers, drying systems and technology: Drying technology. What you get is not just one machine, but multiple machines. Machines that are perfectly adapted to each other. No matter what perspective you take, your production line will benefit from our experience.
Your contact
Contact us now for a personal consultation regarding your spray booth!
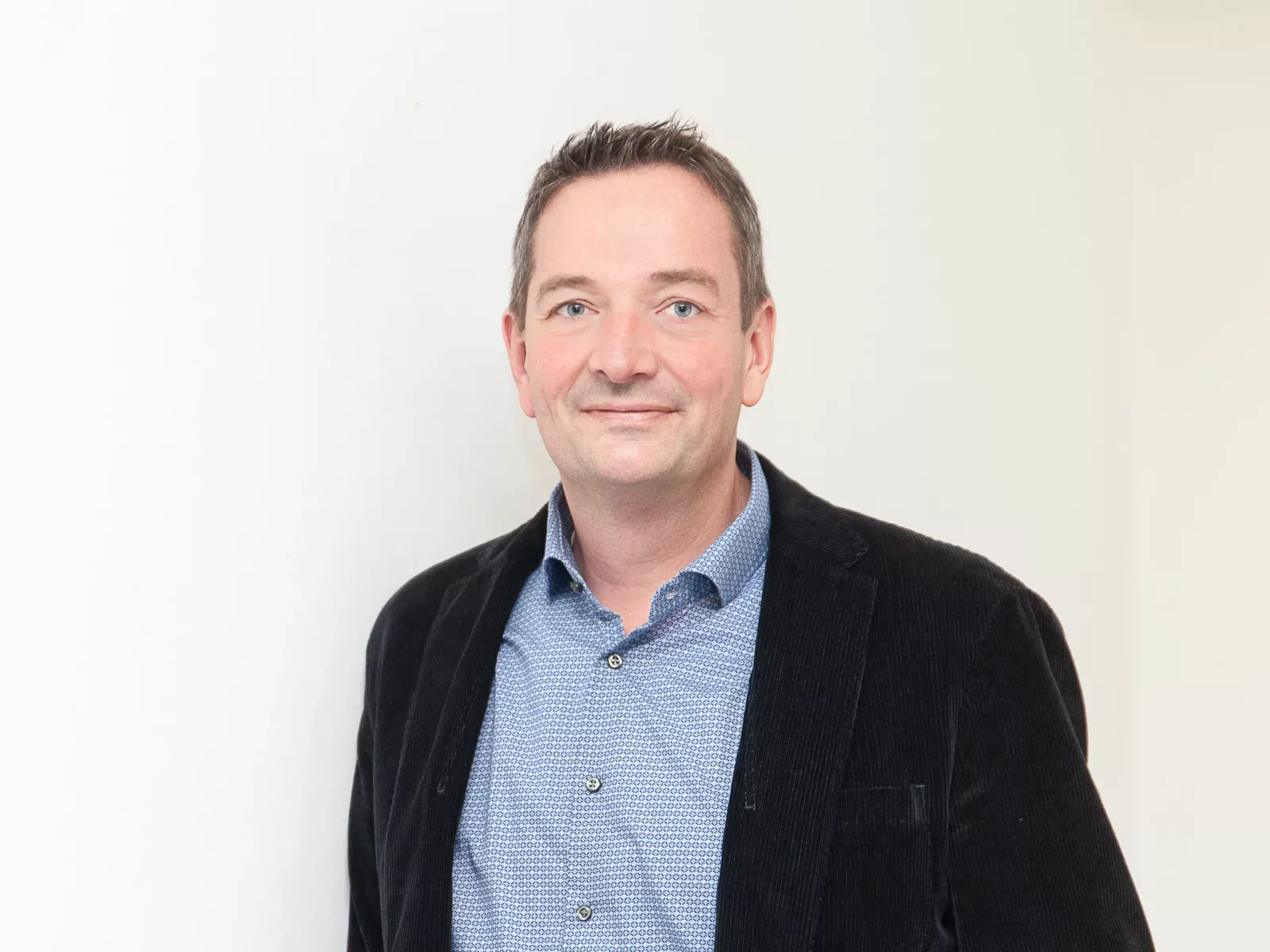
Gert Grosse Deters
General Industry|Automotive
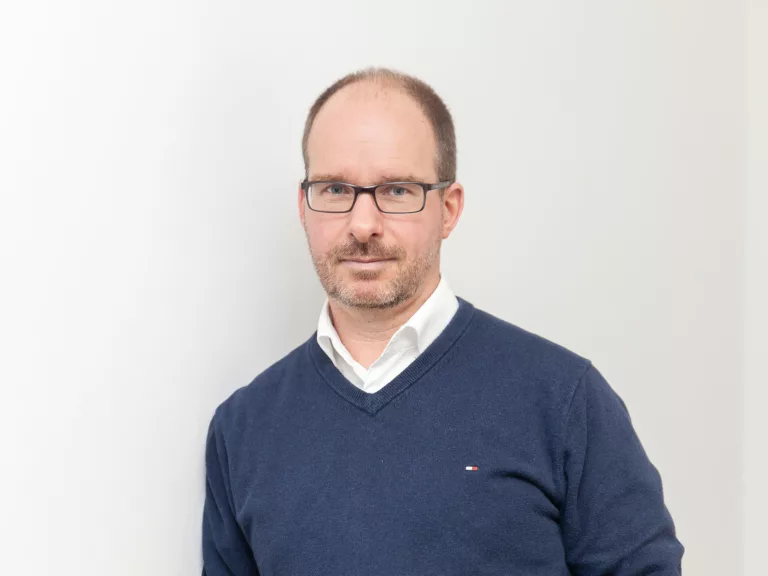
Christian Streit
Wood|Building Materials