Combined fully automated finishing line for white doors
Roller coating and spray coating in a single pass
The Prüm door factory in Weinsheim (Eifel) is now for the first time using an automated finishing line that combines the previously separate processes of roller and spray coating, including all pre- and post-treatments. This enables the door manufacturer to paint its white interior doors twice as fast as before. The quality has also been further improved as a result.
“We make a door white. That sounds simple. But the process is more complex than some people imagine,” says Christof Thielen, Technical Manager at Prüm-Türenwerk GmbH. The company, which is part of the Arbonia Doors Group, specializes in the timeless classic of white doors, among other things. In the course of its multi-year investment process, frame and door production were separated from each other. New machines and systems were largely installed in the door factory. This also included a Venjakob roller and spray coating line, individually designed to meet the special requirements of premium white doors.
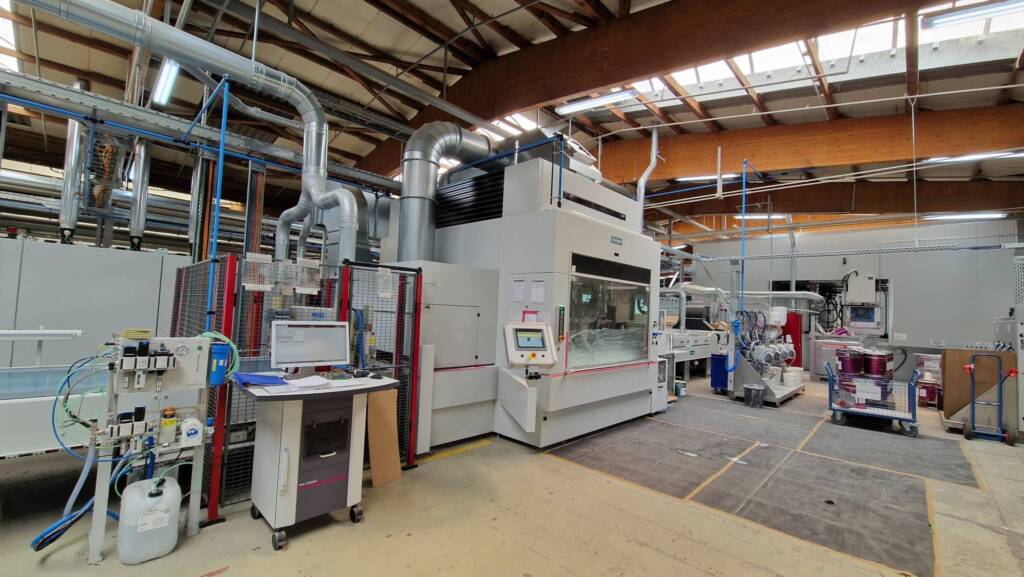
Combined roller spray coating line for interior doors
view of the spray coating machine
Type VEN SPRAY PERFECT with integrated quick color change system.
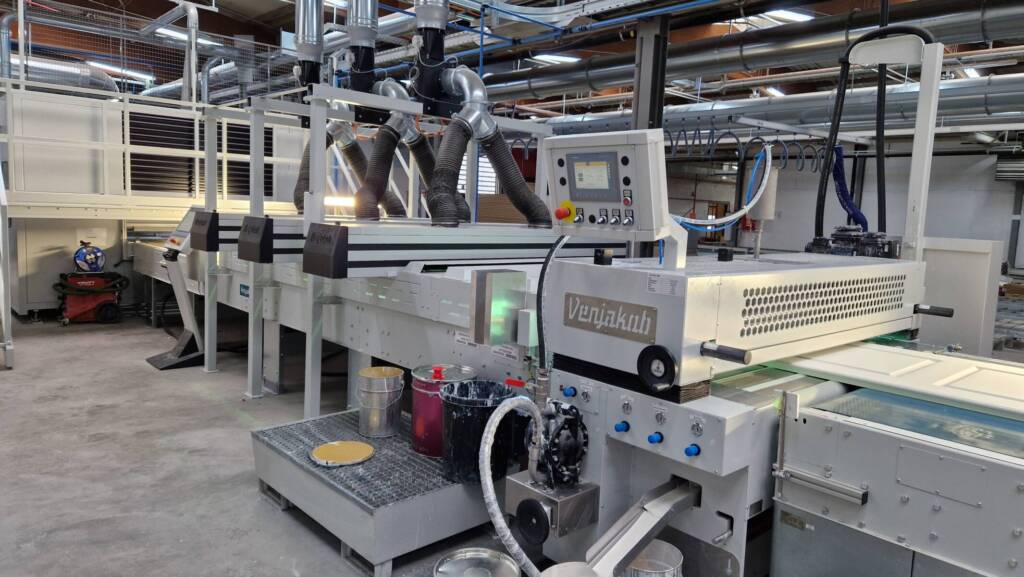
Roller coater and UV channels for curing the UV lacquer
which is applied to smooth and textured door surfaces as a primer using the rollers
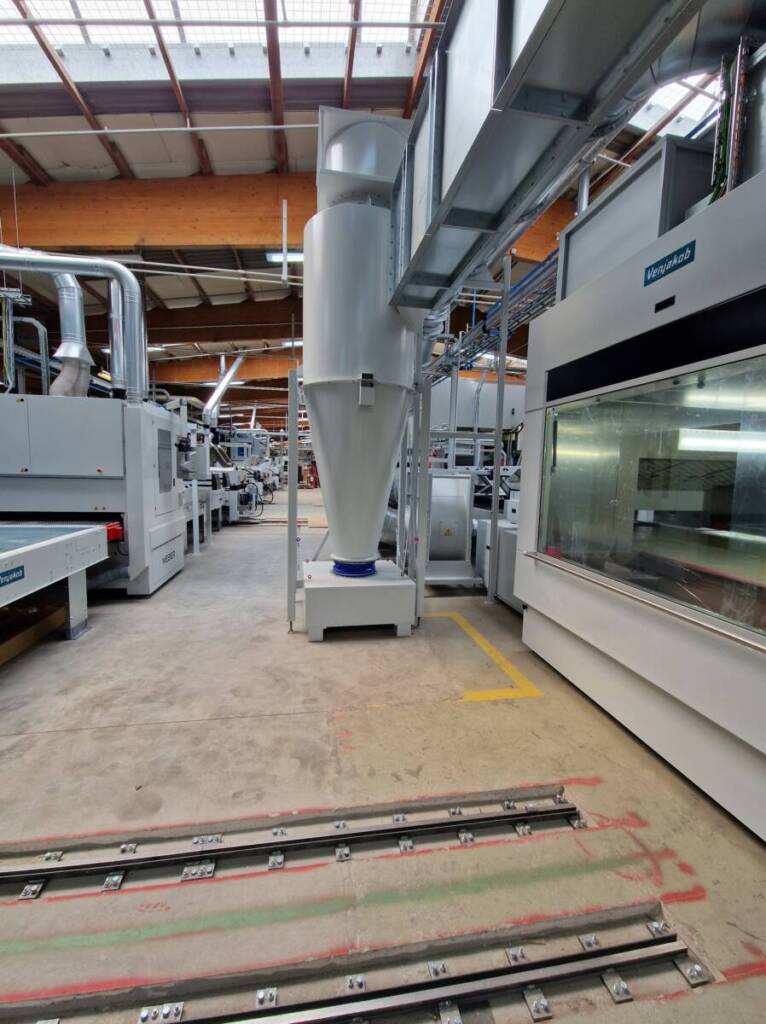
View of the cyclone separator
The cyclone separator specially developed for quick-drying coating materials is more powerful than any conventional dry or wet extraction system. It offers high savings on disposal costs, as no paint sludge is produced. In addition, the use of coagulants and defoaming agents is eliminated and the purchase of filter mats is reduced.
High demands on quality and quantity
Previously, two individual systems were in operation. One for roller coating and priming, one for top coating using the spray process. As the capacity in the white paint area had reached its limits, the company invested in a new painting line. Venjakob was ultimately selected as the premium partner for finishing within the Arbonia Group. The many years of excellent cooperation with Venjakob and the individually designed system solutions, which are already in use at sister companies such as Garant, were the decisive factors in Prüm-Türenwerk’s decision to work with the machine manufacturer. “We wanted to combine both processes automatically in one line. Our requirements were already quite demanding. The different applications, priming and painting, had to be adapted both to the special features of the two exclusive white lacquers and to the quantity to be achieved. The joint project planning process for this took several months,” says Prüm’s Technical Director, Christof Thielen.
Twice as fast as before
Within the coating and priming process, three sanding machines are used for pre-sanding and intermediate lacquer sanding as well as four roller coating machines for applying the primer. A fifth was added as a replacement. The entire roller coating and spraying process, including turning and returning the workpieces for a second pass, comprises 14 production steps.
With this system combination, a time saving of 50% is achieved compared to coating on two separate coating systems.” In addition to the development of the combined roller and spray coating system, including drying technology, the entire conveyor and air technology was also supplied by full-service provider Venjakob.
We wanted to combine both processes automatically in one line. Our requirements were already quite demanding.
Christof Thielen - technical manager of Prüm
Gentle handling of expensive coating material
A good paint finish, as used for interior doors, looks good and withstands many demands. As much of this exclusive white lacquer as possible should be applied to the door. The use of a roller coater is ideal for this. The lacquer applied hits the door 100 percent. No loss due to overspray, as is the case with spray coating. Here, too, the subsequent spray coating process is designed in such a way that as little paint as possible is “missed”. On the one hand, atomization is reduced by conditioning the air in the spray booth, which increases the transfer rate of the paint to the door. Secondly, a specially developed cyclone separator is used to collect the paint waste and thus reduce disposal costs.
Tricky edge sanding
The rabbet and door are painted and sanded in a continuous process. This also applies to sanding the two longitudinal edges and the top edge. As the edges have different widths, the width of the Venjakob edge sanding machine is adjusted accordingly. A moving, diagonal sanding unit is used to sand the leading edge in throughfeed. A trailing unit with three brushes moves along the upper edge as it passes through, creating an impressive image.
Best features combined in one line
All in all, the Venjakob roll-spraying line described above is a proven masterpiece that combines various features to get the best out of the system. For the Prüm door factory, the combined system is an important part of shortening the entire production process. This is also the manufacturer’s declared aim in times of scarce raw materials and supply bottlenecks.
YOUR CONTACT PERSON
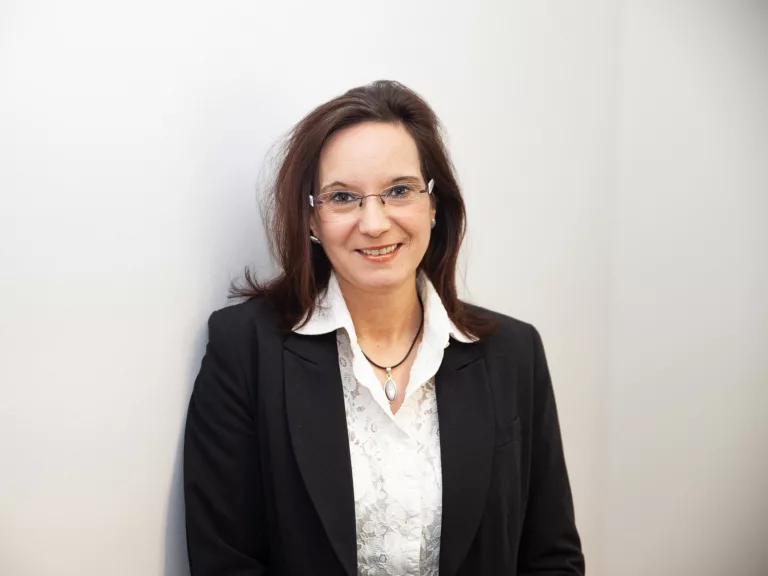