- Venjakob
- Finishing | Coating
- Roller coater
Roller coating with a roller coater from Venjakob | WO-TECH
Whenever you need to coat one or both sides of flat products, wood panels, doors, parquet and other flooring such as LVT and SPC, furniture parts, glass, concrete slabs or any other flat material, roller coating is the method of choice. Typical coating materials are water- or solvent-based coatings, UV coatings, fillers, stains, and various types of adhesives and hot melt glues. Venjakob offers systems to handle any of the processes. We have developed all variants of roller coaters together with our partner WO-TECH – for your specific application. We would also like you to know: If you choose us, you will get your entire solution from a single source. Both for roller coating and for the curtain coating method. In this section we would like to show you what is important for a roller coater, which application methods are possible, which advantages the process offers – and why you are on the safe side with solutions from Venjakob. But let’s start at the beginning.
What are the necessary considerations for a roller coater
A large number of parameters have to be taken into account for roller coating: Working width, output quantity, feed rate, the required surface quality, layer thickness, energy requirements – the entire machine technology must fit seamlessly into your process. No matter what industry you are in: the coating method, the necessary machines and the process must be adapted to each other. One of the most important questions is what material you wish to coat – wood, metal or a different surface. It is necessary to determine a variety of parameters before you can achieve the ideal coating result. At Venjakob we take all these factors into account and settle any unanswered questions with you before we get started.
Roller coaters and curtain coating machines with technology from Venjakob|WO-TECH
Various application methods exist for coating. Roller and curtain coating is used for flat components such as doors, wood panels, floors made of wood or plastic, and furniture parts. Both processes – roller coating and curtain coating – offer specific advantages. The advantages of roller coating are the low-loss material application due to the excellent application efficiency of almost 100 percent; curtain coating, on the other hand, makes it possible to apply thicker layers while maintaining perfect surface quality.
Everything from a single source – from your surface technology experts
100 percent efficiency? That applies to our systems’ application efficiency, but also to our own workflow: At Venjakob we give it 100 percent to be a specialist for surface technology that can offer you everything from a single source. Our portfolio includes a wide range of spray coating systems as well as suitable conveyor technology and handling and drying systems. Our partnership with WO-TECH GmbH – a specialist in surface technology like us, with unique know-how and many years of experience in roller coating and curtain coating technology – allows us to add two additional application processes to our spray coating portfolio: roller coating and curtain coating.
Combined processes for the best surface results
What is true for all our coating solutions applies here, too: We develop customized solutions especially for you. What that means is that, depending on your requirements, we combine roller coating and curtain coating machines with other coating processes as well as surface pretreatmentand drying systems, but also with modern handling solutions in a sophisticated, user-oriented comprehensive system solution. That is how we ensure that our customers achieve the best possible surface results through targeted surface and edge application and overall high coating performance.
Roller coating: Application and advantages
Roller coating permits single-sided and double-sided coating of flat workpieces. An application roller applies the required fluid – be it lacquer, filler, stain or glue. The advantage of roller coating is the low-loss application of coating materials. In fact, as previously mentioned, the application efficiency with this coating process is almost 100 percent. This means that almost 100 percent of the lacquer, the stain, the coating medium ends up on the object being coated. And only there.
Coating – for what purpose, with what material and with what type of roller
Single-sided, double-sided, with lacquer, filler, stain or glue – the fields of application for roller coating are manifold.
Suitable workpieces for roller coating
- Doors
- Furniture parts
- Wood and plastic floors
- Wood-based panels
- Glass
- Concrete slabs
- Flat workpieces of all kinds
Suitable application media for roller coating
- Water- and solvent-based or UV-curing coatings
- Fillers
- Hot melt adhesives
- Various glues
- and many, many more
Roller coater variants:
- Roller coater (coating on one side|both sides)
- Filler machine (coating on one side)
- Hot melt machine (coating one side)
- Glue application machine (coating on one side|both sides)
Curtain coating – applications and advantages
The curtain coating process is perfect for coating flat workpieces on one side. A conveyor belt transports the workpieces through a curtain consisting of liquid coating material. This coating material curtain comes from a curtain coating head and is deposited in a homogeneous layer on the workpiece surface. The curtain coating process is used primarily for applying large quantities, for stringent demands on surface quality and for partially shaped surfaces.
Filler machines, glue application machines and other modern roller coating technologies
As a Venjakob customer, you benefit from sophisticated, cost-effective comprehensive solutions. Modern equipment for roller coating is available from us at Venjakob and our partner WO-TECH. Our systems are sturdy and long-lived. The modular structure makes it possible to design the roller coating system precisely according to your requirements. In addition, it permits adaptation of the coating line to your requirements and product specifications, and expansion whenever you need it. Even after the sale of a system solution, we are always ready to serve you. We provide nearly instant service and support through state-of-the-art communication technologies. And if you do end up needing us to be there in person, we will come to your location.
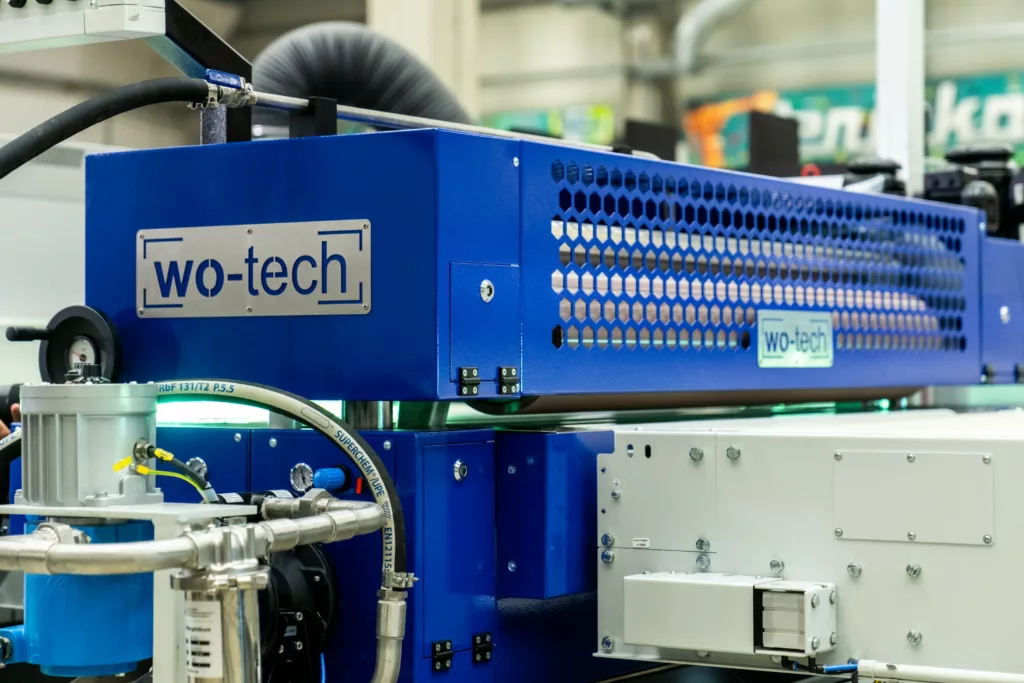
Roller coaters
Roller coaters achieve great efficiency in coating application, are easy to clean and ensure high output rates.
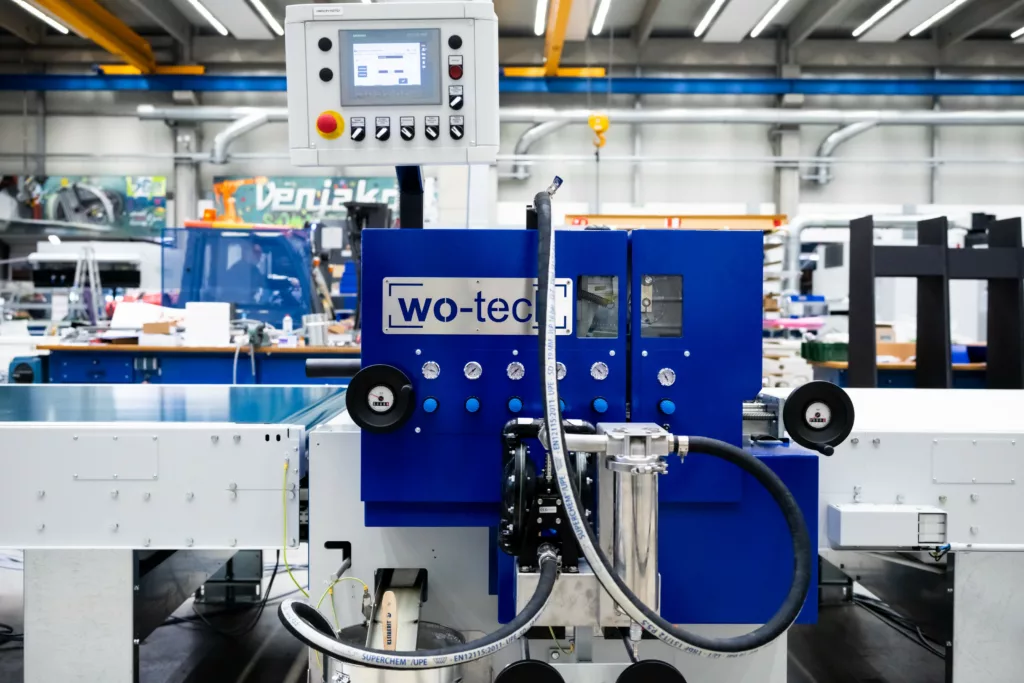
Filler machine
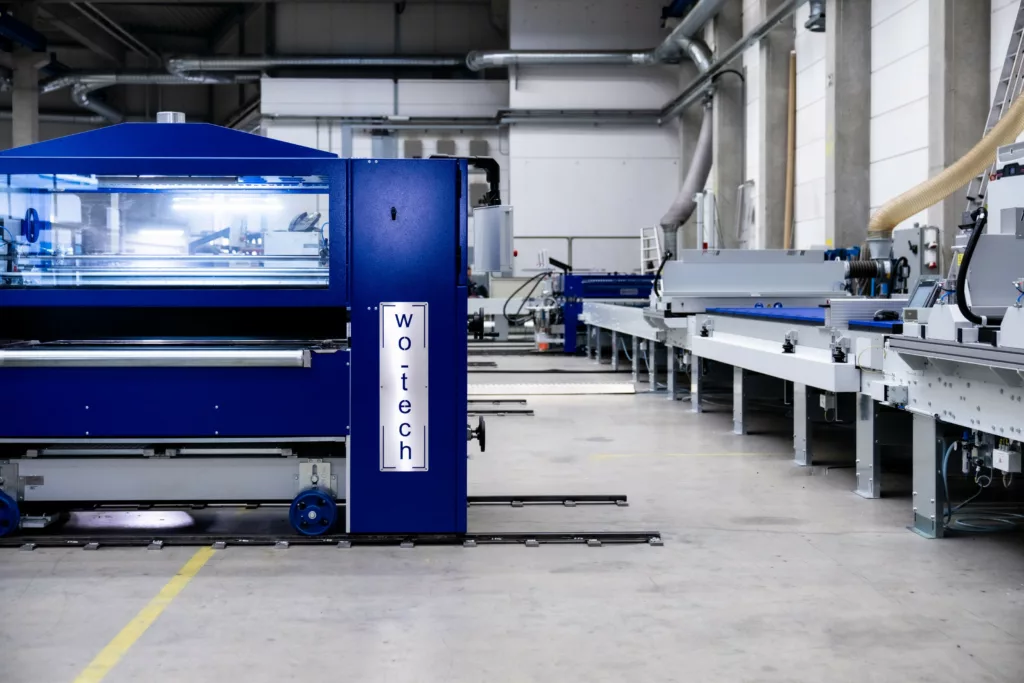
Hot melt application
Special machines are required for the application of hot melt adhesives. Whether as a visible layer for appearance or as an adhesive functional layer, precise application is necessary. Hot melt adhesive machines achieve excellent coating quality thanks to uniform heat distribution. They form a good foundation for a multi-layer build-up or optimal bonding. The hot melt application machine can be combined with suitable components to form an entire plant, perfect for the application of decorative or functional films or the production of sandwich elements.
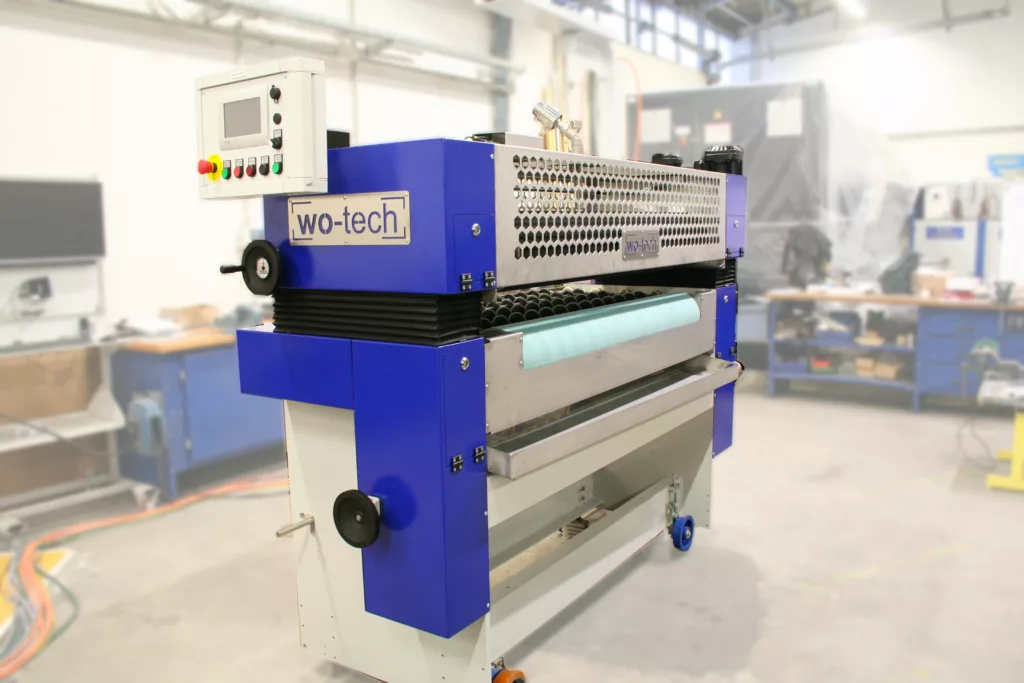
Glue application machine
Custom-designed plant technology for roller coating as your key to success
The modular design of our systems makes it possible to develop customer-specific solutions. Systems for surface pretreatment and drying, added as needed, create perfect surface quality and permit rapid further processing after the coating process. Handling systems adapted to the required output quantities and workpiece properties ensure optimum utilization of the equipment. They are always individually adapted to the coating material used and the workpiece being coated. Venjakob offers a broad portfolio of different coating system concepts.
A comprehensive approach with modular flexibility
None of our customers need every single component in our portfolio. That should go without saying. That is exactly why we can’t think in terms of products. Instead, we focus on variability, flexibility and modules that can be combined according to specific requirements. It is not unusual for us to develop special solutions for specific cases to meet every single requirement of an order. The very first step is our initial contact, during which you describe your requirements in detail. We figure out the future location at which the system will soon be performing your desired task. Next comes the conceptual design: What would you like the system to do? What performance requirements are we looking at? What type of application do you need: Roller coating? Spray coating? Combinations of different application methods? What types of machines can be used within the coating system to create a cost-effective concept while simultaneously optimizing output?
The advantages:
- Modular system concept: We develop customized solutions for each and every requirement profile.
- Easy to integrate and expand: We offer the modules to create a complete line for you, including pretreatment systems, drying systems and handling technology.
- Flexible adjustment: We offer optional components such as pumps and filling systems.
- High reliability: High application accuracy across the entire working width.
- Secure processes: Low-vibration coating and long service life due to high-quality design of all components.
- High economic efficiency and plant availability: Greater efficiency thanks to low-maintenance, service-friendly technology.
- Simple operation: Intuitive, modern control technology.
- Quick cleaning: Easy handling, quick changeover and fast cleaning go hand in hand.
- High availability: The plants are designed for efficiency.
- Ergonomic, easy handling: Working height, feed rate and all other parameters are perfectly adapted to each other.
- Wide range of applications: Our solutions have proven their worth in numerous industries and on a wide variety of substrates for decades.
- Reliable partnership: We constantly invest in research and product development, have over 60 years of experience in surface technology and offer fast service with high spare parts availability.
Service and support? You’ve got it, with our app!
Service and support are among our top priorities. We provide advice, technology and equipment – as well as the spare parts if you need them. We guarantee that you can get in contact with us at any time. In short: you can rely on us. Before you ever get your system, we test it at our technical center. After your system is fully implemented, we remain at your disposal. We take care of maintenance. Service and support is provided by Venjakob Digital Service via the Oculavis AR service app, which offers video calls with augmented reality. Meaning: It’s practically like having us right there with you (only without travel expenses and long journeys). Why not download our app right now?
Long-term investment security through Venjakob plant technology
As a high-performance partner for a wide range of industries, we implement solutions for your specific requirements. The Venjakob modular system also allows existing plant technology to be flexibly adapted to new conditions and requirements at a later date. You benefit from long-term planning and investment security.
So what’s next? Are you considering adding a roller coater to your business?
Let's summarize the most important facts one more time: When coating flat materials, wood or metal, or different surfaces with their specific requirements, or surfaces that have damaged areas, the best solution is a machine that achieves reliable coating results through roller coating. As a finishing specialist whose approach is to provide advice independently of technology we work with you to determine which solution is right for you. That’s what you get with Venjakob. We offer you plant technology for a whole range of different processes. If roller coating is the only solution for you, then you will discover that we’re the perfect partner to design your system for you. Even in this case, we use not only our own know-how, but also the experience of our partner WO-TECH. This way, you get the know-how of not one, but two specialists – but from a single source. And this applies to the complete plant, because we offer you exactly the modules that make sense for your production and meet your requirements, from handling and conveying systems to pretreatment and drying. What’s especially great about our systems is this: They let you grow with your challenges. Retrofitting and expansion of your system is possible at any time.
DOWNLOAD AREA
- ROLLER COATING LINE FOR SOLID COLOR FURNITURE COMPONENTS
- COMBINED COATING LINE WITH SPRAY AND ROLLER COATING
- ROLLER COATING LINE FOR WOODEN FLOORING
- THE CURING OF UV-COATING MATERIALS
- COMPACT ROLLER COATING LINE
- HOTMELT LAMINATING LINE
Your contact
Our in-house technical center makes it possible to test processes under realistic conditions. Simply tell us what you need, get your material supplier involved, and we will develop a solution together with you.
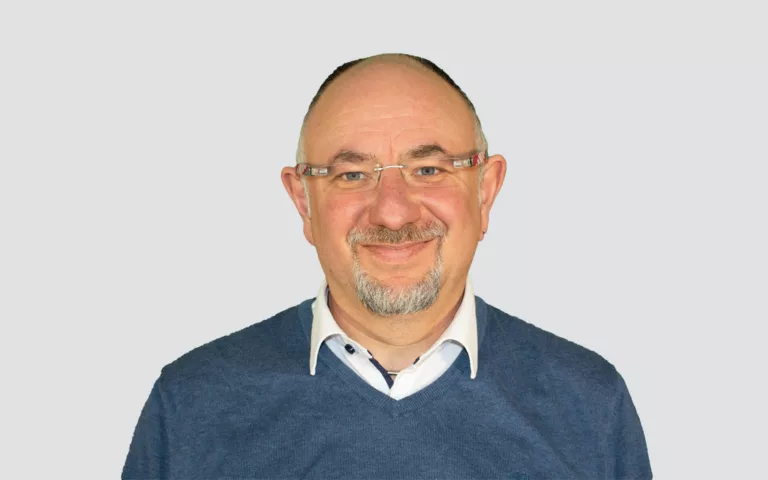