- Venjakob
- Areas of application
- Plastics coating
Plastics coating with Venjakob
Plastic items are a huge part of our everyday lives. Just as there is no one polymer, but different polymers, not all plastics are the same. The variety of material compositions and shapes is too great and the demands for the final surface vary too much for us to present all possible system variants right here. What you need to know is: Venjakob offers a comprehensive portfolio of systems for surface coating. We will find a customized solution for your application, for your production, for your manufacturing process. For coated plastic products, for any surface. Whenever you need to coat plastic, you can count on our process experience.
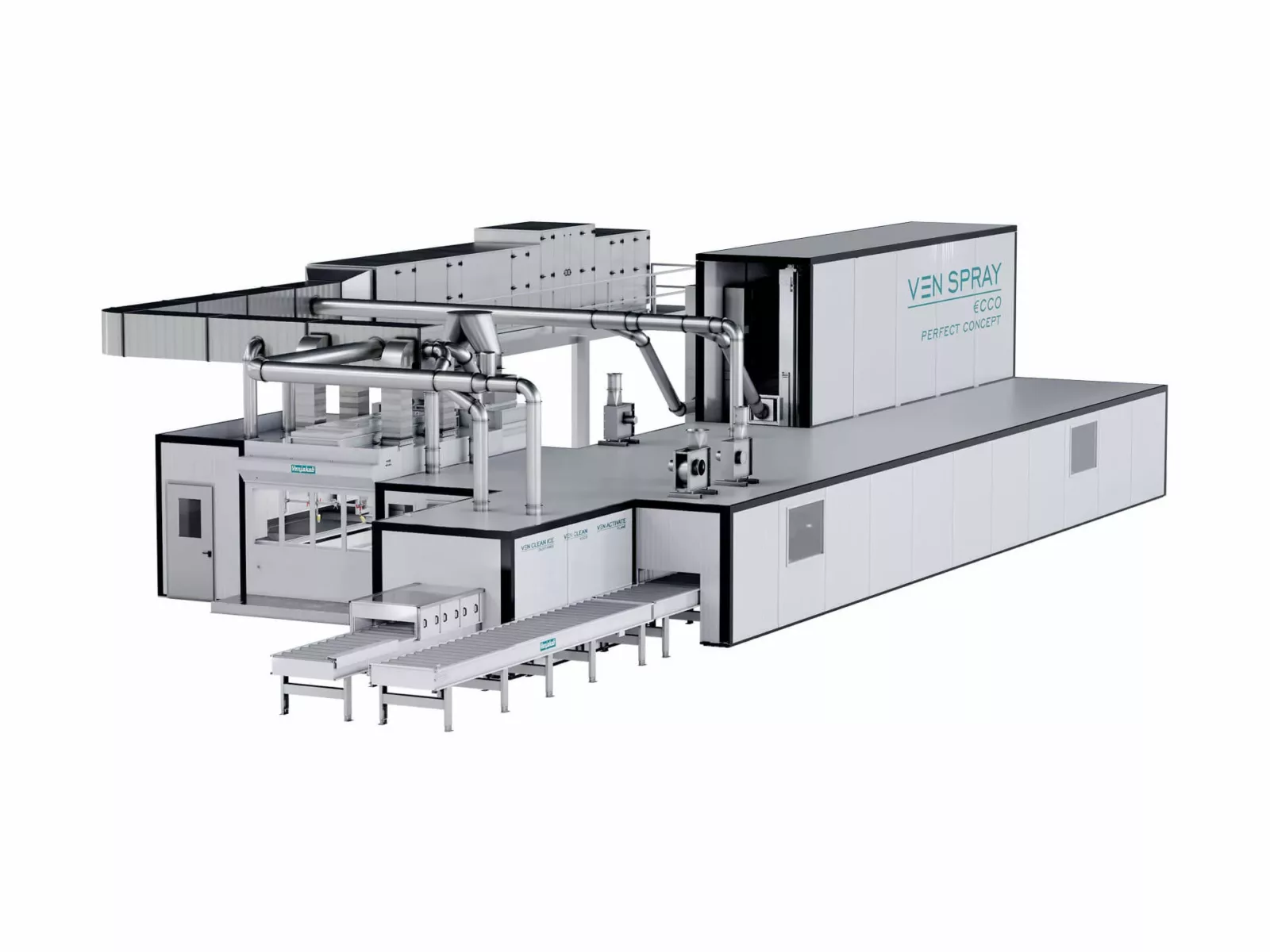
Venjakob system concepts for surface finishing of various plastics
What factors need to be coordinated when designing your coating system? What coating do you want to apply to the surface? What are the properties of the material? How adhesive are the surfaces? Which process offers the greatest advantages for your specific application? These are the questions we answer – together with you and your coating material supplier. Let us give you an overview of three types of plastic coatings.
Functional finishes
- for weather protection – against UV rays|moisture
- to improve scratch and abrasion resistance
Decorative finishes
- Day & night design
- Metallic effect finish or high-gloss piano effect
- Substitutions for electroplating looks
Effect finishes
- Changed feel: Lacquer like leather – soft touch
Perfect surface finishes for plastics
Unlike almost any other material, plastic permits a wide range of processing and finishing options. With specialized equipment for applying functional finishes, you can change the surface of plastic components entirely according to your requirements and, just for instance, use effect finishes to imitate the feel of leather. Other coating processes are used to protect components against the elements.
Coating plastics – from metallic look to day and night design
Custom-made Venjakob systems can be used to apply a wide variety of decorative finishes. As experts in the field of industrial finishing, we design systems that let you create metallic effects through coating, i.e. they make your coated plastic products look like metal. In addition, you can create high-quality day and night designs. That is a special surface technology for plastics in which high-contrast designs are lasered into plastic surfaces, which, when backlit, ensure great legibility even at night. Components processed in this manner are often found on the dashboards of cars or on electrical household appliances.
Applying functional finishes with modern production lines
Venjakob has decades of experience in the field of surface finishing of plastics and has satisfied numerous customers in the automotive and automotive supplier industry with its high-performance, reliable system concepts. Venjakob finishing systems in use in the automotive industry improve the appearance of car interiors and exteriors and protect components from UV radiation, scratches and abrasions with special coatings.
Functional surface finishes for plastic components are also used in numerous other industrial sectors. The following examples are only a small excerpt. As an innovative partner of industry, Venjakob has implemented significantly more system concepts than presented here.
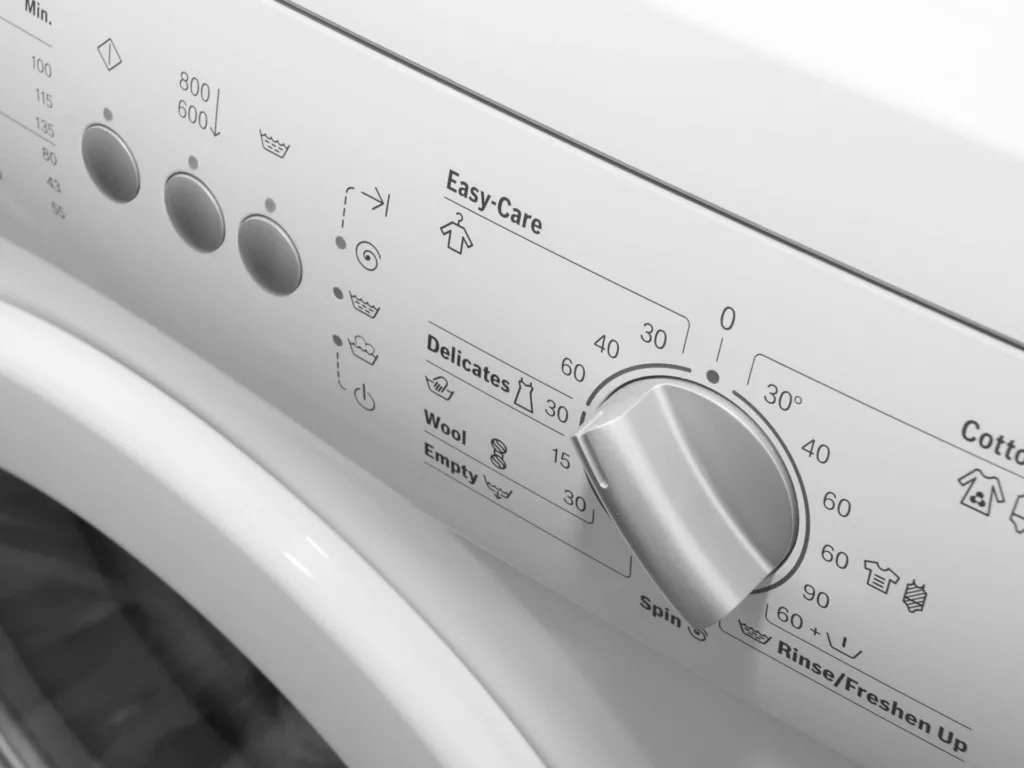
Home appliances
Is there anything you use more often than a washing machine or dishwasher? When you think about that, you’ll hardly be surprised to find that appliance coatings have to meet high standards. A wide variety of system concepts are in use in the small and large home appliance and electrical industry sectors, for instance for coating appliance panels and housings. They differ in their conveying method: continuous, linear, rotationally symmetrical.
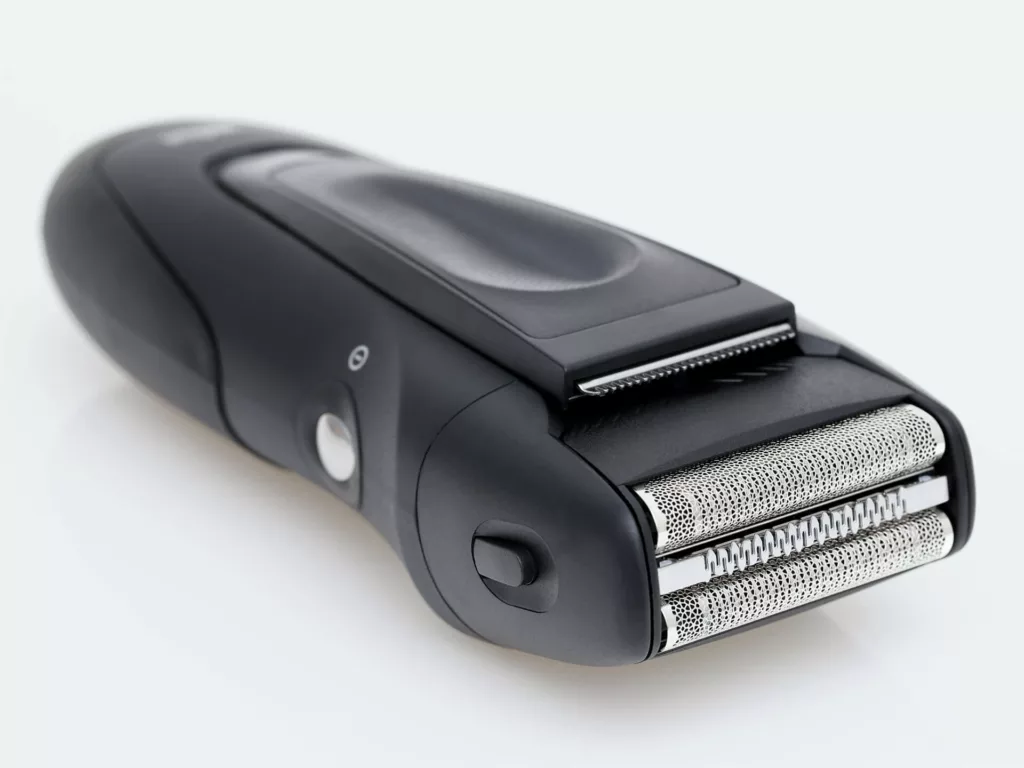
Small appliances
The demands that have to be met by small electrical appliances such as shavers are similarly high as those in the large appliance sector. These small appliances have long since ceased to be merely functional, they also have to look good. The care products used during shaving pose a special challenge to the surface (chemical resistance). This, combined with ensuring that the surface remains appealing in the long term (value retention), is highly complex. A wide variety of coating systems are used for this purpose and require special system concepts.
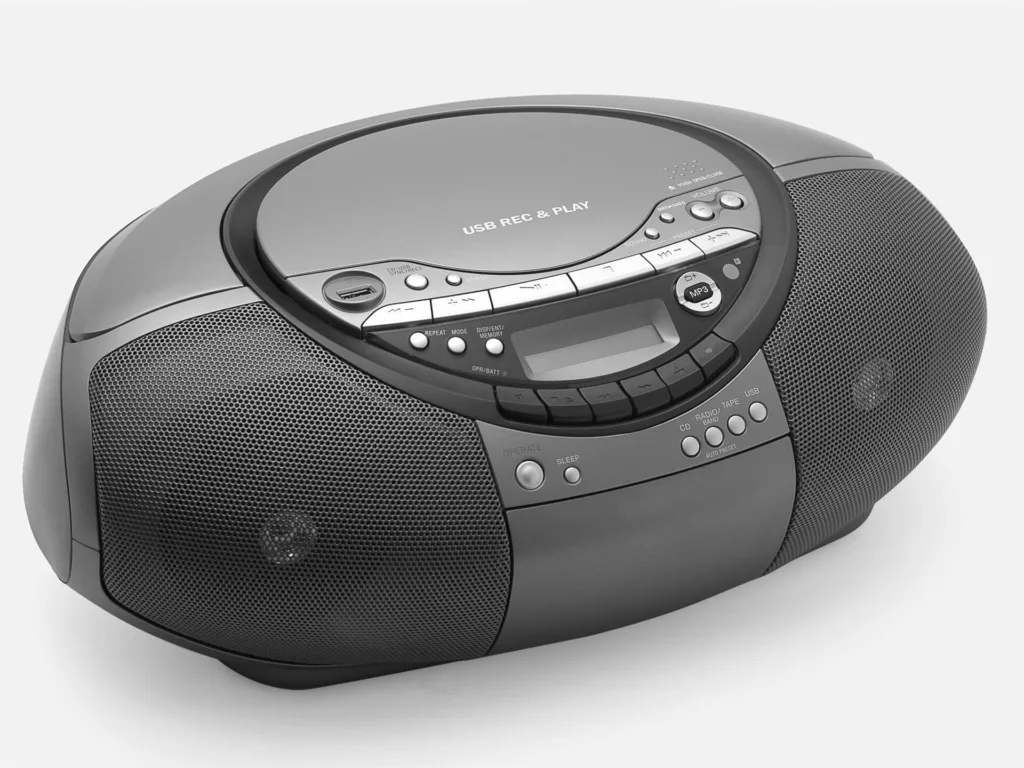
Entertainment electronics
Entertainment electronics is a generic term that covers everything from a portable player to the high-quality music system around which music enthusiasts sometimes design their entire home. So what that means is: The surface has to show the special quality of the product. Frequent use of the product means that maintaining the attractiveness of the surface can be a challenge (scratch and abrasion resistance, resistance to finger sweat and lotions).
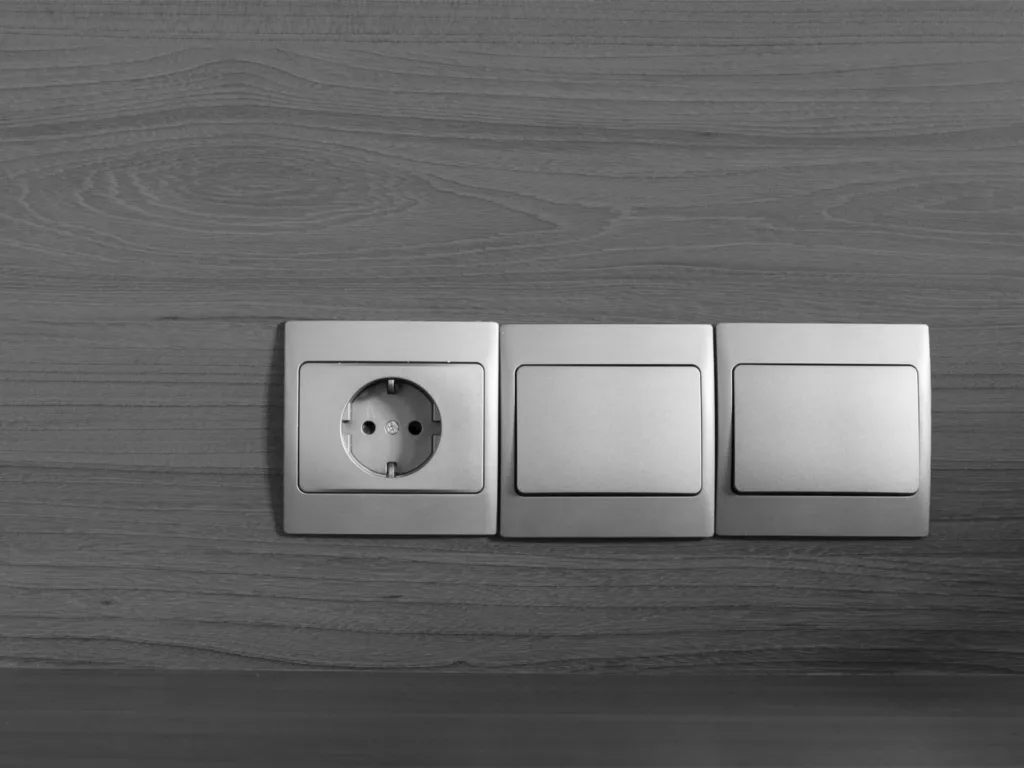
Household technology
Household technology is a broad field that includes all the things plugs and switches have to handle in a home, from luxury designs to mass-produced goods. It includes both small batch sizes, especially for project-related furnishing of apartments/houses, and series production in large quantities, e.g. for DIY stores. Special demands are placed on the surface in terms of color design, feel, scratch resistance, finger sweat and creams - and these are met by a variety of coating systems.
We provide specific advise for each application and offer you the perfect solution. Both as stand-alone systems and as complete coating lines including components for surface pretreatment, coating, drying, automation or exhaust air purification. Feel free to contact us at any time to discuss customized system concepts for use in your production!
Advanced surface technology for plastics
As you can see: All that glitters is not metal. Much of what looks like it is actually made of plastic. Coated plastic, specifically. In fact, so many things are made of plastics with different finishes that most of us no longer even think about whether the items underneath the finish are plastic or metal or wood. But at Venjakob, we think hard about it. In fact, you could almost say that we hardly ever think about anything else as much as we do about how a finish can act in such a way that the actual workpiece appears as if it were made of metal or wood. This is basically true for all our Venjakob coating solutions. Coating plastic is just one special case. Why is that? You can find out here.
What is plastic coating all about?
There are materials that are so beautiful that their beauty should not be hidden and affected by a coating. That’s not the case for plastics. Hardly anyone is fascinated by the aesthetics of plastics. But we are. That’s because we know how tremendously versatile the practically uncountable varieties of plastics are. They make it possible to create, shape and design almost anything you could imagine. In a wide range of hardnesses. In almost any desired look. In almost all sizes. After all, these materials are called “plastics” because of their versatile plasticity. That’s why we believe it’s perfectly reasonable to be fascinated by plastics and their applications. At Venjakob we are quite proud to have the process experience to give these plastics the final touch they need through coating that makes coated plastic products what they are: high-quality products, durable solutions that make our everyday lives better.
The value of plastics coating
There are at least two answers to the question of why plastics have to be coated in the first place. First of all, for appearance reasons, because the workpieces are part of a larger product and have to match it. Take, for instance, plastic fittings as part of white goods (washing machines, dishwashers) or automotive applications – inside and out. Secondly, to protect the coated material – for example, from the elements in outdoor applications: As corrosion protection, for example, at the joints of plastic parts and metals. Or to ensure UV resistance or to guarantee abrasion resistance. We would like to add a third answer to these two, which may already be included in the first two, but still underlines the true importance of plastics coating: It’s the coating that truly emphasizes and completes the full product value of the coated product – and it contributes significantly to maintaining this value in the long term. In short: The surface coating is both protection and expression of beauty, as well as a guarantee of quality.
In conclusion: Plastics coating is one of the most fascinating fields of application
To summarize: Plastics coating is as versatile as the variety of plastics that can be coated and all their possible applications in and of themselves. Protection, beauty and maintaining the value of the coated product are common responses to why coating is required. But beyond that, coating – and this does not just apply to plastics coating – is not just an add-on to the product, but an essential part of its function and finish. A car without a paint job – and that includes its coated plastic parts – may still be a car, but it’s an incomplete one. The same basically goes for all coated products.
This is precisely why there are no standardized recipes for how to coat a component. The areas of application and the options for developing solutions are simply too diverse. The workpieces, the production process and the intended use of the products place demands on the coating process that cannot be solved simply by selecting the best coating material, the best lacquer or other medium. This requires comprehensive solutions that start even before the surfaces are pretreated and do not end with drying and packing. At Venjakob, we specialize in this comprehensive approach. The result of decades of development for our company in almost all areas of industrial coating is, what we believe to be, a unique process experience. This means that, in Venjakob, you will find a partner who looks beyond the coating line – and takes the whole of your production into account.
We hope that we have answered the basic questions of what types of plastic coatings exist and why plastic needs to be coated at all in this overview. We would be happy to answer any specific questions that relate to you and your production in a personal conversation. Let’s talk! About the coating processes you need, the equipment we can design for you, and our experience in combining the two to best effect, when creating your custom-developed Venjakob coating solution.
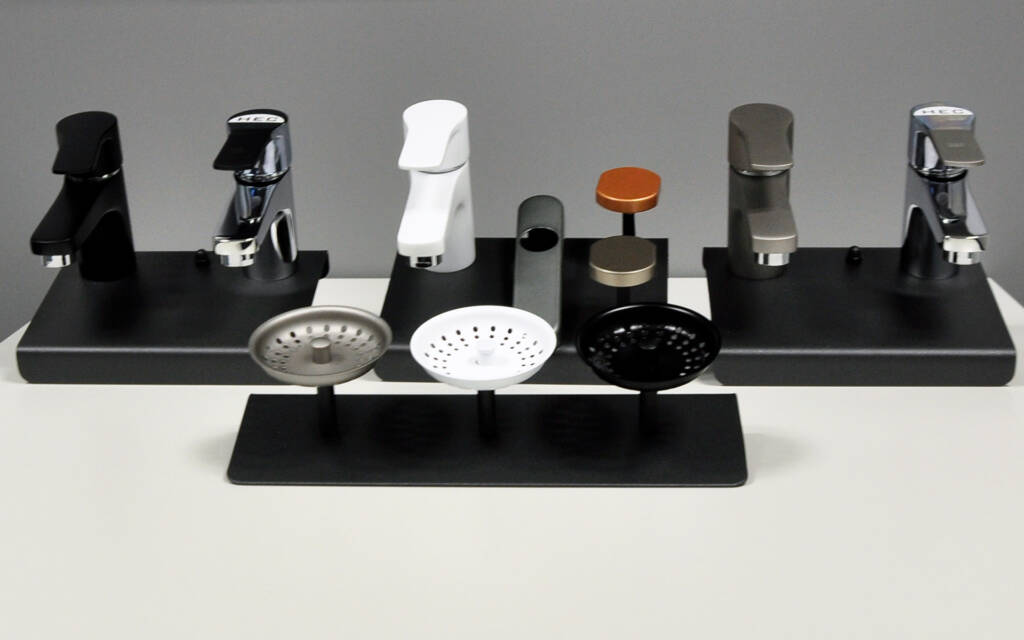
Reference companies that use our solutions
-
Dr. Schneider Group https://www.dr-schneider.com/
-
Vogler Industrielackierungen https://www.vogler-gmbh.com
-
Kostal Group https://www.kostal.com/de-de/
-
Vulkoprin https://vulkoprin.de
Your CONTACT
Interested? Then let’s talk! About a special solution for any application – or more generally about the plant that will help you get ahead.
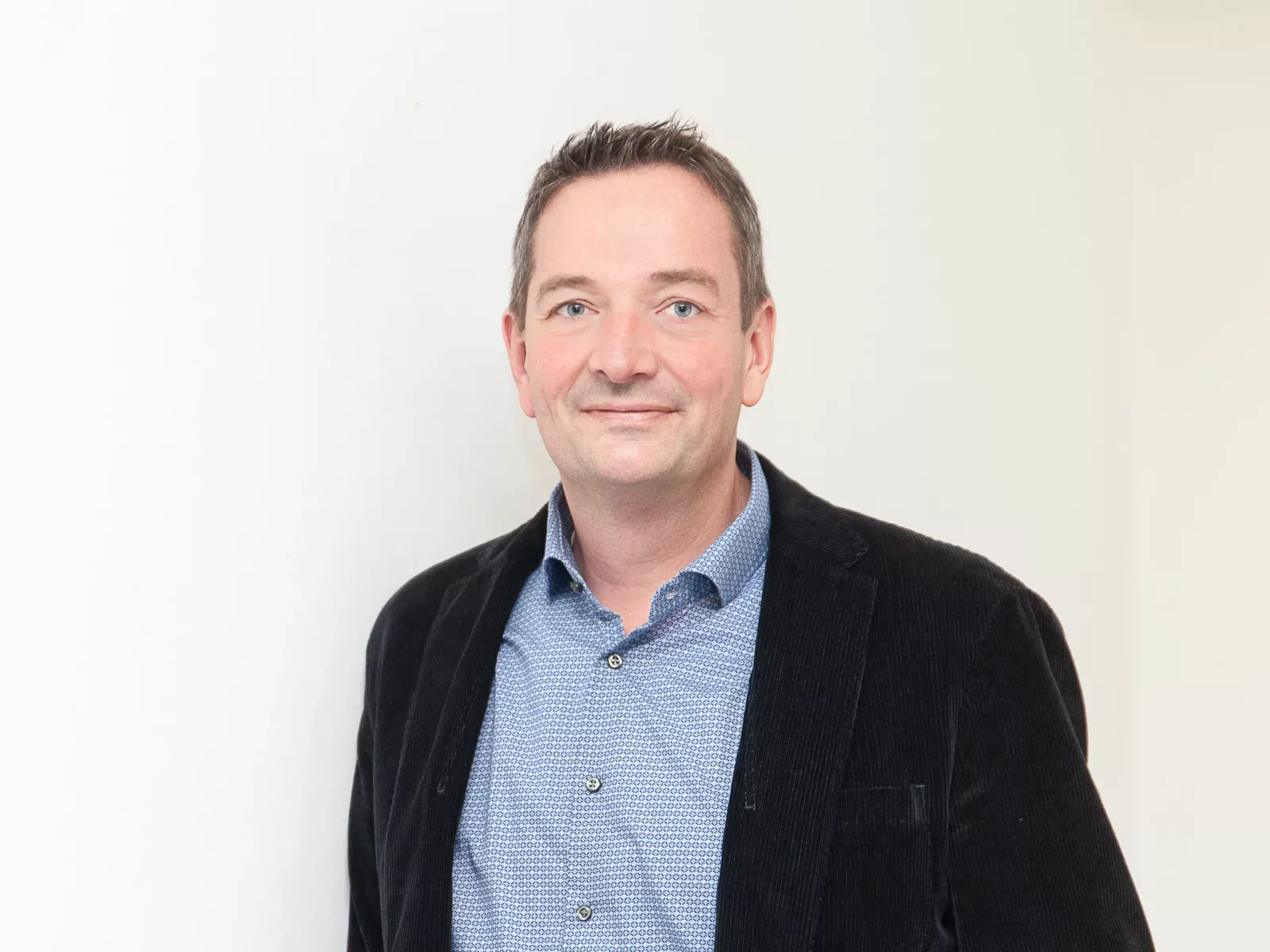
Gert Grosse Deters
General Industry|Automotive