- Venjakob
- Surface pretreatment
- Activation process
- Plasma
Plasma activation with Venjakob
Venjakob offers plasma activation, an excellent method for surface modification that optimizes the surface to promote perfect finish adhesion. But what exactly is plasma activation? What does it do? How is it done and what do you need to keep in mind when doing it? Generally speaking, plasma activation changes the surface of a product about to be coated in a way that provides better adhesion for the coating. For instance plasma removes particles that contaminate materials about to be coated – particularly very small contaminants. In concrete terms, this requires a supply of energy, which causes a change in the aggregate states from solid to liquid and gaseous to plasma. This process creates surface tension with polar-charged molecules, to which coating materials can connect so that their adhesion is improved. The result: thorough cleaning and excellent preparation for the coating process – that’s what plasma activation does. But let’s start at the beginning.
Surface modification with ionized gas
Plasma activation with ionized gas guarantees particularly efficient surface modification, e.g. of plastics, metals or composite materials. Plasma activation modifies the surface energy precisely and selectively exactly where it is required. Oxygen plasma can also be used for cleaning – for example, to prepare the surface for adhesives that are applied in a later step. Oxygen can be combined with other gases – this is recommended, for instance, when etching surfaces. In general, the result of plasma activation is a significantly better surface wettability. This creates the ideal conditions for subsequent coating of the workpieces and materials. Among surface pretreatment processes, plasma is only one activation process along with flame treatment and flame silicification.The different varieties of plasma activation
Plasma activation is a process that comes in a variety of forms. The different methods include the atmospheric pressure method, corona treatment and activation by low-pressure plasma.
Atmospheric plasma can be generated under normal pressure. The advantage is that you do not need a low-pressure chamber. A special nozzle technology introduces the potential-free plasma directly into the production process under normal pressure conditions. The results are comparable with low-pressure plasma. The process is used industrially in the cleaning and activation of metals and plastics. The integration of the process into existing production lines is relatively straightforward in terms of costs – also due to the absence of a low-pressure chamber. It is particularly suitable for applying coatings to metals to protect against corrosion and improve adhesion. And this is usually done without solvents. The process is therefore also environmentally friendly. It can be used for plasma cleaning of continuous metal profiles, pipes before coating, painting or further treatment with adhesives. The process is also suitable for robots.
The surfaces of many plastics – for example polypropylene – are usually water-repellent and electrically well insulated. Wetting with paints, varnishes and other coating materials such as adhesives or bonding agents is therefore very problematic. What helps here is the so-called silent electrical discharge with DBD plasma. DBD stands for Dielectric Barrier Discharge. Treating the material surfaces with a dielectric barrier discharge plasma increases their surface energy and therefore also the adhesion forces of the surface. These adhesion forces increase the attraction between the molecules of the treated interface layers. Put simply, this increase significantly improves wettability. It is precisely thanks to this effect that activation by means of corona treatment is used industrially in the production and finishing of materials. In fact, it is one of the most common processes.
Low-pressure plasmas are used in various technical applications – for example in the manufacture of microelectronic components and in the finishing of surfaces. Another field of application is coating technology. Venjakob also uses this plasma treatment process. When generating low-pressure plasma, the pressure is considerably lower than the earth’s atmospheric pressure. They are operated in the pressure range of just a few pascals and are classified as non-thermal plasmas. The treatment of components takes place in a special treatment chamber, the low-pressure chamber.
Areas of application
Plasma activation is used in the following fields:
Goals of plasma treatment
- Ultra-fine cleaning
- Increased wettability
- Improved adhesion
Use
- Plastic
- Metal
- Composites
The advantages of Venjakob plasma systems
At this point we could say that the advantages of a Venjakob plasma system are flexibility, flexibility and flexibility. First, because the modular design makes Venjakob plasma systems easy to integrate into existing plants and production lines – whether they are continuous flow systems, robot systems or spindle chain systems. Second, because it’s available as a stand-alone solution, if that’s what you are looking for. And third, because every solution we offer is customized – tailored precisely to your production techniques, plant technologies and requirements. But flexibility is obviously not the only advantage: Of course, the real benefits are the top-quality this method achieves:
- Ultra-fine cleaning: The finest contaminants, the finest deposits, barely visible or even completely invisible dirt don’t stand a chance – simply activate with plasma and the surface is cleaned – thoroughly! To put it simply: Plasma can be used for ultra-fine cleaning in a variety of ways. Another method is the use of plasma-vacuum technologies, that is, the low-pressure method, which has the advantage of cleaning much larger surfaces.
- Increased wettability: Plasma treatment ensures that material and molecules are open for optimal wetting. All treated materials are ready for a coat or finish.
- Optimized adhesion: Plasma treatment significantly improves the adhesion of coatings. The reason for this is that the plasma modifies the surface during treatment. The surface of the object treated with plasma becomes smooth due to the increase in surface energy. This, in turn, improves the adhesion properties of the coating.
- Ultrafine cleaning: The finest impurities, the finest deposits, barely visible or even invisible soiling don't stand a chance - simply activate the plasma and the surface is cleaned - thoroughly. In other words: plasma can be used in various ways to carry out ultra-fine cleaning. Another method is the use of plasma-vacuum technologies, i.e. the low-pressure process, which has the advantage that it can be used to clean much larger surfaces. Increased wettability: Plasma treatment ensures that the material and molecules are open for optimum wetting. You are ready to paint and coat all treated materials.
- Optimized adhesion: Plasma treatment significantly improves the adhesion of paints. The reason for this is that the plasma modifies the surface during treatment. The surface of the object treated with plasma becomes smooth due to the increase in surface energy. This in turn leads to improved adhesion and bonding properties of the paint. Increased wettability: Plasma treatment ensures that the material and molecules are open for optimum wetting. You are ready to paint and coat all treated materials.
Stand-alone or part of a line – but always completely customized.
We have mentioned it before, but perhaps some more detail would be helpful: Your Venjakob plasma system is also available as a stand-alone solution. Or Venjakob can offer you a complete start-to-finish solution incorporating feeding, the necessary pretreatment, which includes plasma activation, followed by the actual coating system itself, as well as drying systems and exhaust air purification. All components are perfectly coordinated – from loading to discharge. Venjakob can offer you a complete start-to-finish solution incorporating feeding, the necessary pretreatment, which includes plasma activation, followed by the actual coating system itself, as well as drying systems and exhaust air purification. All components are perfectly coordinated – from loading to the continuous chain conveyor system or throughfeed system to discharge. The design process always includes all possible aspects of process optimization, whether it’s parameter control or throughput speed, self-cleaning steel belts or easy cleaning of the spray booth.
Let’s talk – about plasma activation and your Venjakob system
To explain briefly, plasma activation is a technology that optimizes and cleans surfaces. It is also frequently referred to as plasma treatment or plasma cleaning. Mostly it is used in the treatment of various materials such as plastics, metals or organic substances. In simple terms, plasma activation involves an ionized gas, the plasma, that generates a strong electric field to affect the surface of the material being treated. Plasma activation increases the surface energy of the material, making it easier for various chemical compounds to dock to the surface. Three methods can be used to do so – treatment with atmospheric pressure plasma (also called AP plasma), with DBD plasma (referred to as corona treatment), and finally the low-pressure plasma method, in which the plasma is generated in a specially designed low-pressure chamber. Plasma activation is integrated into the surface pretreatment phase, which is followed by the actual coating process – for instance spray coating. At Venjakob we are happy to offer you plasma activation as a stand-alone solution, should you request and require it. But in general we always recommend a complete solution including feeding, pretreatment, coating, drying, exhaust air purification and removal. All our custom-developed solutions are tailored to the quantities being produced, the optimum use of coating materials and, of course, the use of energy. Another advantage is process optimization, which simplifies operation and subsequent cleaning for you and your technical personnel and allows you to perform the occasional maintenance task. Should it be required, we will support you not only before implementing your order, but also afterwards.
There’s one thing that is even more important than plasma activation. Trust.
We have told you quite a bit about plasma activation. What we didn’t give you, because we wanted to spare you the dull details, are the technical specifications about wetting optimization and the physical formulas that describe in general terms what, in a specific application, always results in customized solutions. It’s much more important for you to know this: At Venjakob we have been developing and implementing coating systems for six decades. There’s an easy answer to the question of how many of them feature plasma activation: a great many. We have tested the process thoroughly – and continue to test it on an ongoing basis in our technical center. What we mean to say is: Your trust in us is more important than any formula. We would like to invite you to visit us in Rheda-Wiedenbrück to see our quality for yourself. Get in touch with us. We won’t just find any solution – we will find yours.
Your contact
Our in-house technical center makes it possible to test processes under realistic conditions. Simply tell us what you need, get your material supplier involved, and we will develop a solution together with you.
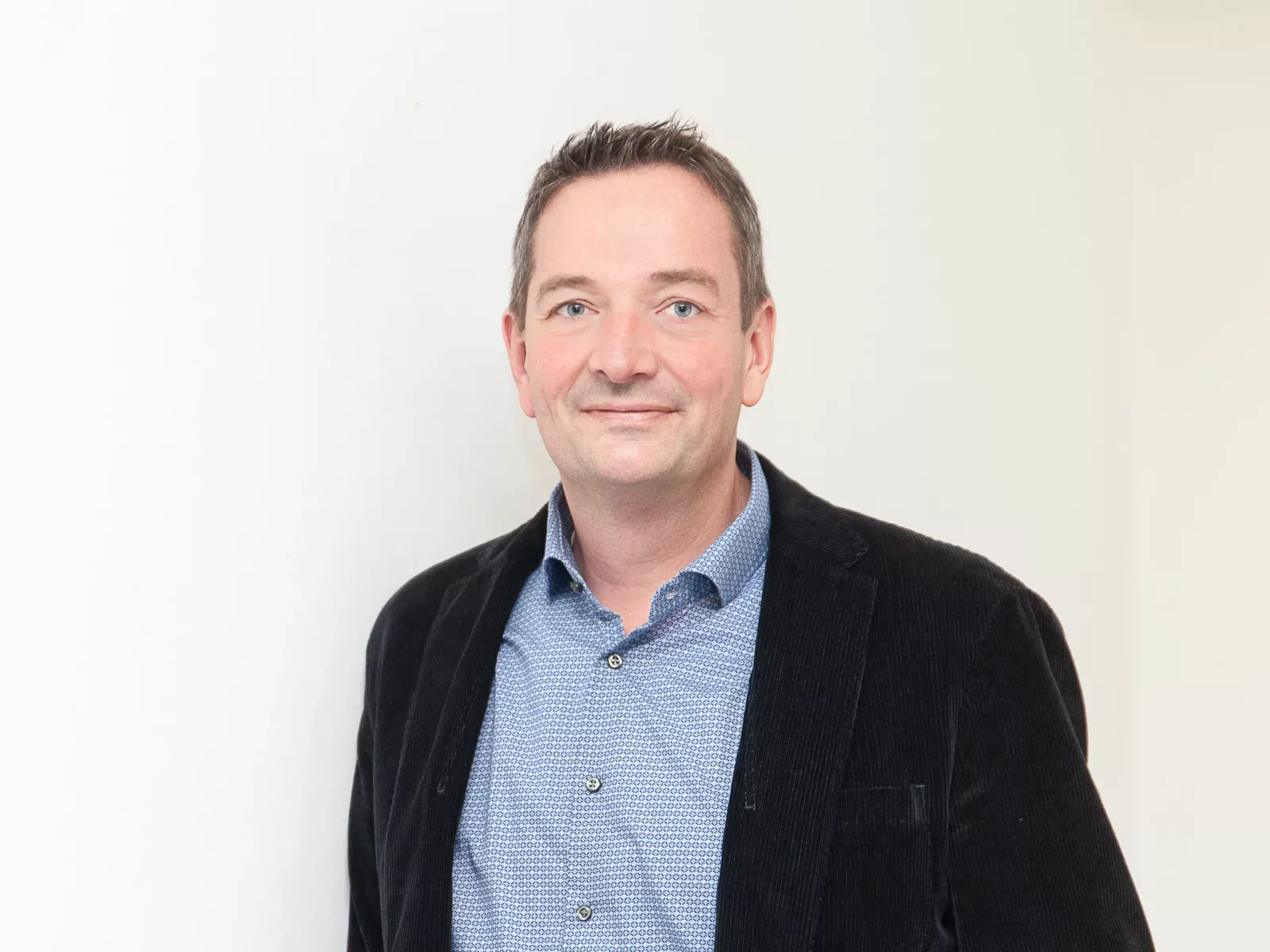
Gert Grosse Deters
General Industry|Automotive