Flexibility more important than utilization
Coating solutions for workshops are less about machine utilization and more about flexibility, speed, and reducing the workload of the few employees. Since this year, the Kalmbach joinery has been painting with Ven Spray One – a semi-automatic coating solution. The latest development from Venjakob is geared to the requirements of the skilled trades. The machine’s delivery time of only four weeks was another important decision criterion for Stephan Kalmbach.
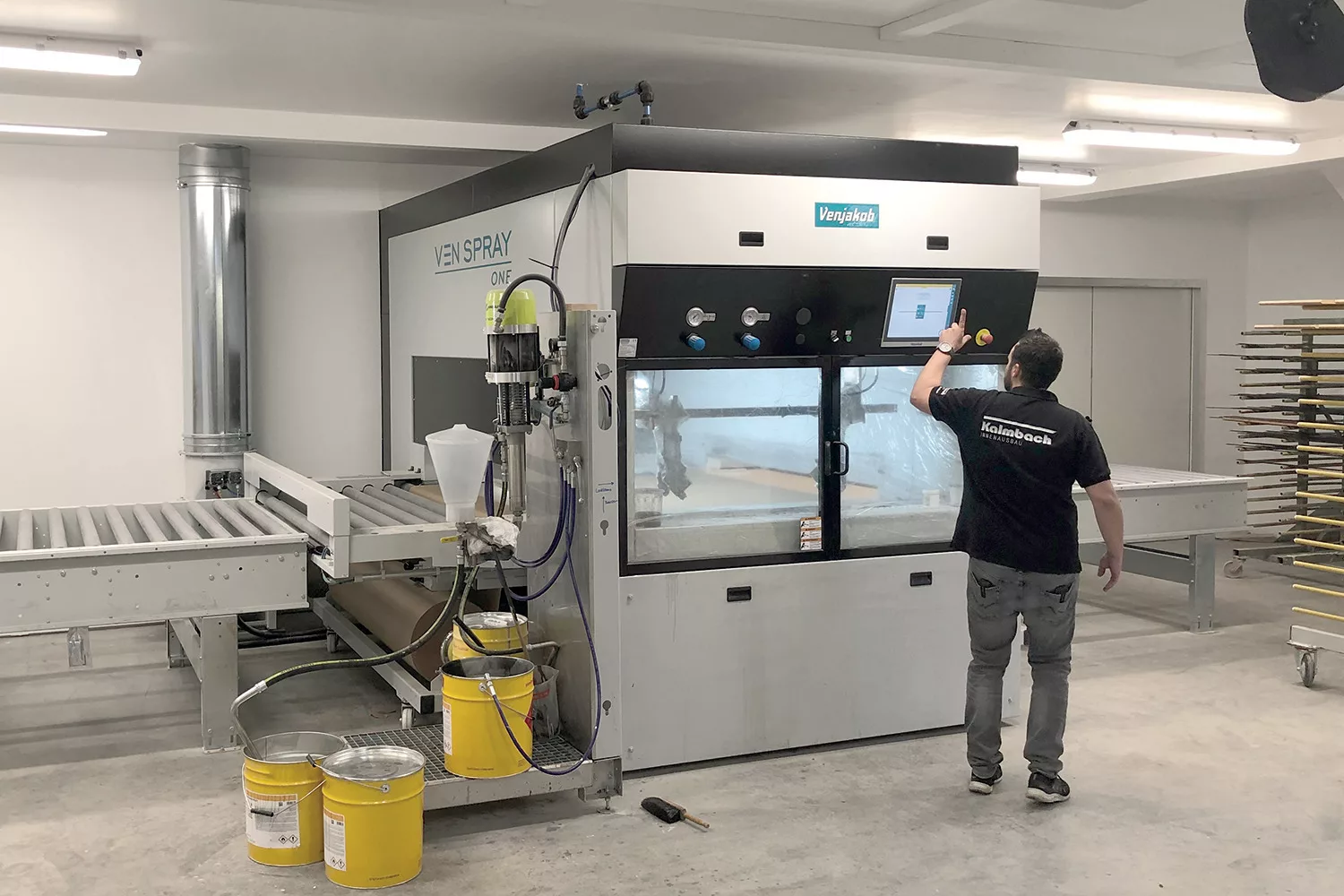
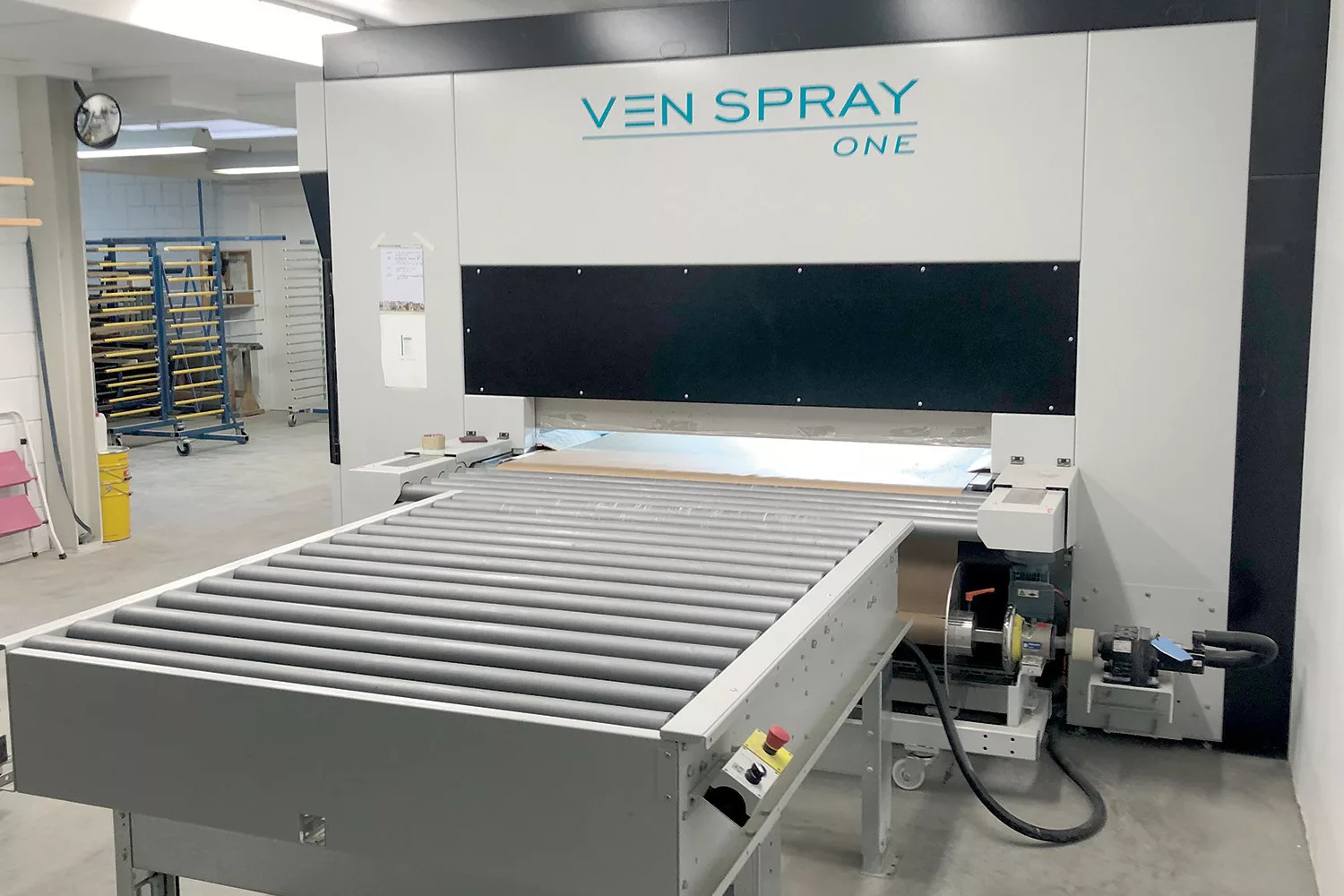
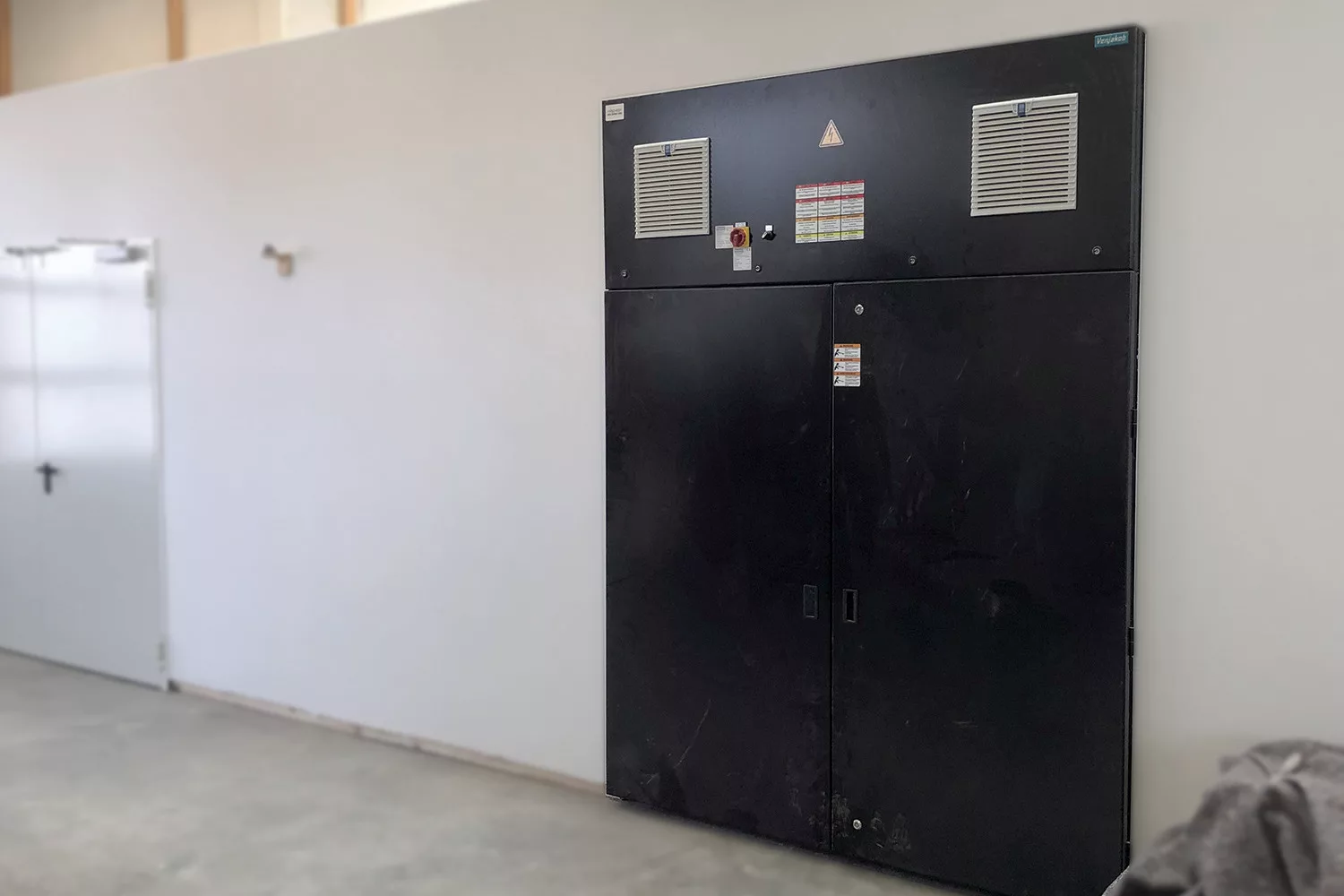
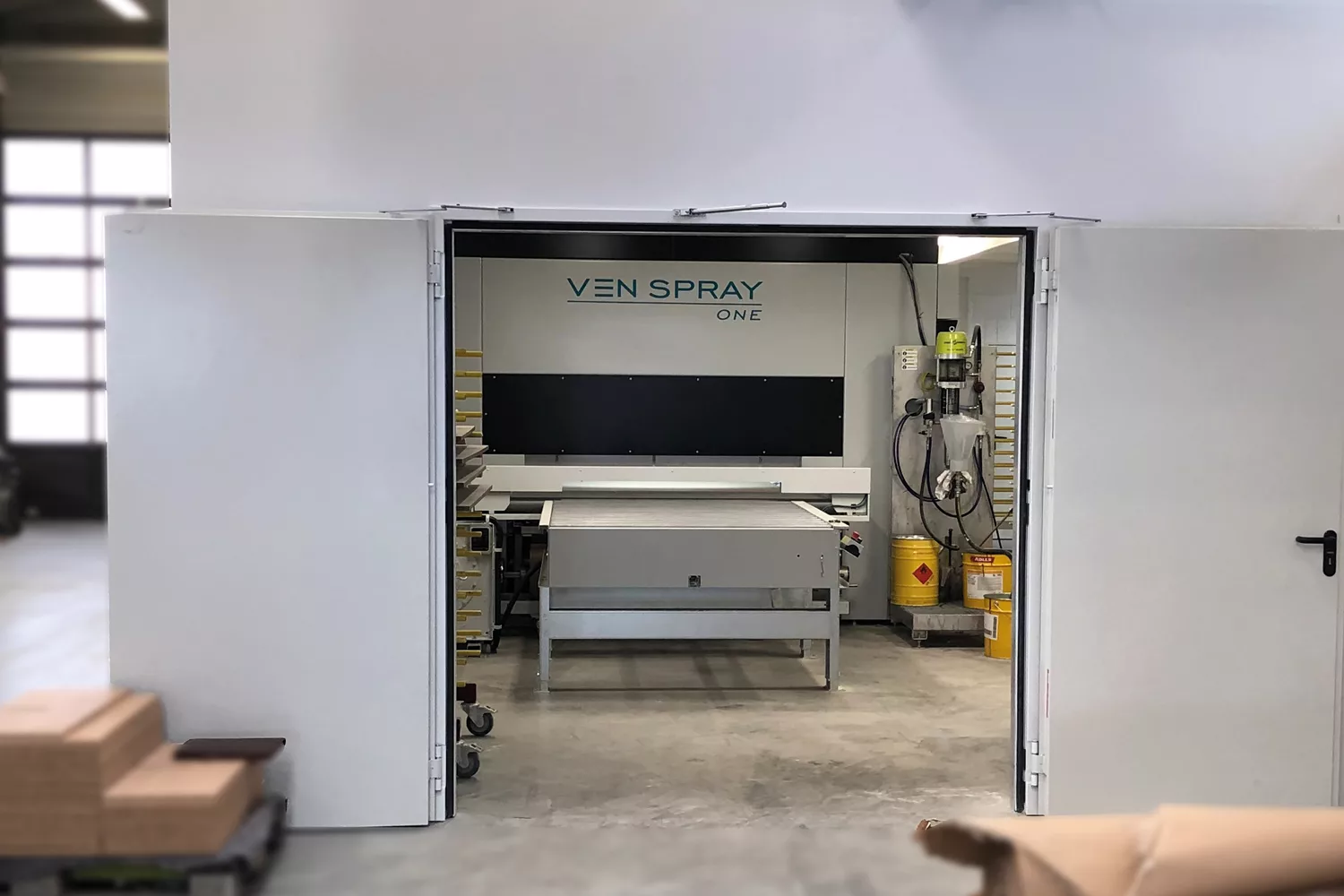
Uncomplicated, flexible and fast – this is what the interior fitter Kalmbach is known for among its customers, who come from all over Germany. The medium-sized family-run business, located in the tranquil town of Simmersfeld, a health resort in the Northern Black Forest, is managed by Rudolf and Stephan Kalmbach. Across an area of approx. 2500 sqm, 20 employees are engaged in the high-quality processing of woods. These subsequently convey a stylish feel-good ambience to the interiors of hotels, clinics, wellness facilities, and high-end restaurants.
Diversity the order of the day
In a joinery of Kalmbach’s size, various objects are in line for surface treatment every day. Sometimes wide wooden panels, sometimes many narrow profiles are finished. Part geometries depend on the interior construction projects. The coating materials used, are also different. Everything still had to be painted and stained on the manual spray booth by the beginning of 2022. “Our Surface department was permanently overworked. We were already considering purchasing a spray coating robot before Covid-19 hit us. But, as always, we didn’t have time to deal with it,” Stephan Kalmbach recounts in retrospect. With the new year, things should be different. Therefore, master joiner Stephan and his father Rudolf Kalmbach together used the time around the turn of the year for initial research into a supplier for a suitable finishing solution, one of which was the company Venjakob. “Admittedly, even as a little boy, my heart beat for Venjakob spray coating machines. But they were out of our league,” admits Kalmbach with a smile. With the Ven Spray One, the finishing system specialist Venjakob launched a single solution for semi-automatic coating on the market in 2020, which is also affordable for smaller companies and is oriented towards their requirements. The Ven Spray One coats using four spray guns that are uniformly controlled by a powerful linear drive. The workpieces to be treated must be at least 25 mm wide and a maximum of 1300 mm.
Short delivery times was one of the decisive factors
The decision to go for the Venjakob machine was based on several factors. “When we decided to invest in a machine, we wanted everything to happen quickly. Only Venjakob could promise us the desired delivery time of four weeks,” says Stephan Kalmbach, praising the entire process. First, Venjakob organized a visit to a joinery in southern Germany so that the Kalmbachs could experience the automatic spray coating machine directly in action. “Nothing was too much for our contact at Venjakob. We were even able to call him during his skiing vacation. From the slopes, he organized a weekend visit for us at short notice to the Venjakob technical center at the company’s site in Rheda-Wiedenbrueck.” At the technical center, Stephan and Rudolf Kalmbach measured the machine in detail. They found that the designated space in the plant was not enough for the machine. Another solution was required.
With its new coating system, Venjakob aims to specifically meet the requirements of cabinet makers and trade businesses. Tim Stender, Venjakob Maschinenbau
Machine intelligently integrated
Now it was a matter of using the remaining four weeks during ongoing operations to make room for the new spray coating machine. “In doing this, we knew that we would set up the painting machine first and then build the room with drywall around it.” Kalmbach came up with a special feature for the integration of the new spray coating machine, which was installed and commissioned within the promised four weeks. The wall at the rear of the machine with the workpiece output has been given a mirror. The purpose of this is to allow a single machine operator to keep track of everything from input to output. The operator feeds the parts to be coated to the machine on the front side via a driven 1.8-meter roller conveyor and sees in the mirror when the workpiece comes out of the machine finished and coated. A roller conveyor was also mounted at the rear. “This makes loading and unloading faster and easier. It is also more cost-efficient because the entire transport width of the coating system can be used. Otherwise, you would have to feed each part individually,” explains Tim Stender, sales engineer at Venjakob. He points out that it is difficult to take full advantage of the working width without a roller conveyor, especially with longer components, because you have to wait until most of the workpiece has been pulled in by the machine before you can let it go. During this time, it is not possible to insert other parts. Those who have the space available should therefore use a powered roller conveyor for loading and unloading, Stender recommends.
Half the time saved
The conclusion around four months after commissioning the Ven Spray One is that it provided real relief all along the line. “We have significant time savings in the finishing process. Things that used to take three to four days at the manual spray booth are now finished in 1.5 days. And that in consistently high quality. We can now use the freed-up capacities of our employees in different areas. The Venjakob salesman was also pleased with Stephan Kalmbach’s statement that the coating machine fulfilled far more than promised. “For example, we do not give a general promise for the processing of stain. To do that, we would have to do test runs beforehand. At Kalmbach, they tried it themselves and were fully satisfied with the results.”
YOUR CONTACT PERSON
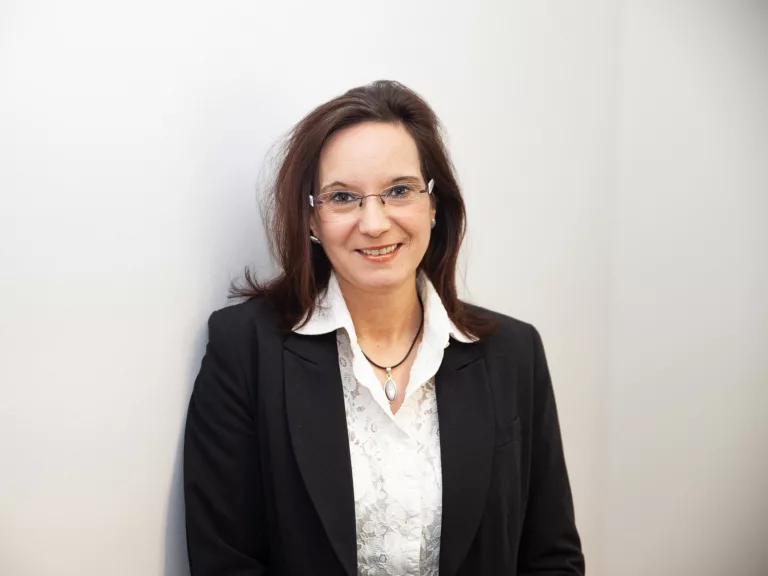