- Venjakob
- COATING LINE FOR STEEL PROFILES AND METAL SHEETS
COATING LINE FOR STEEL PROFILES AND METAL SHEETS
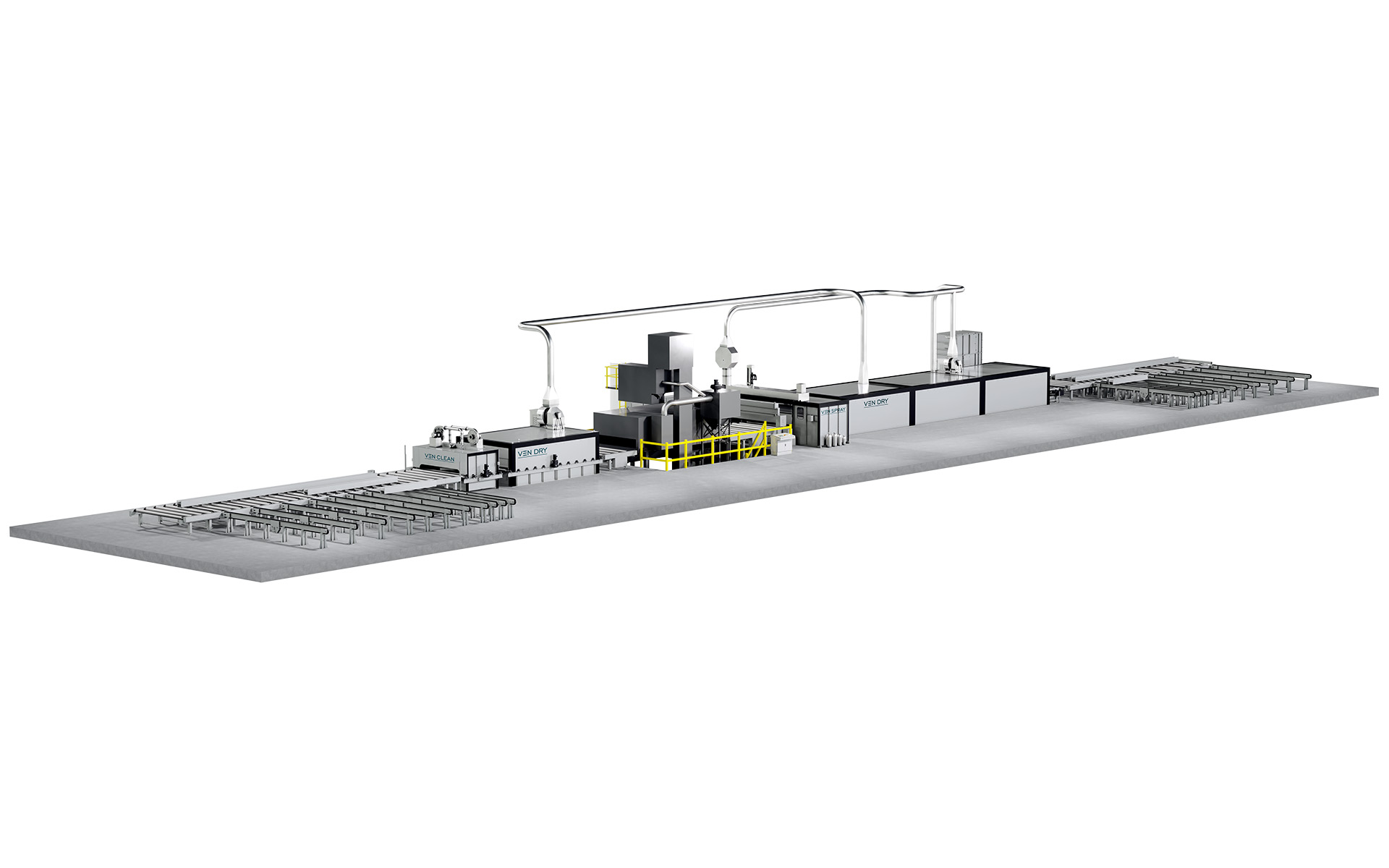
Coating systems for preservation I Final coating I Drying
Steel sheets and steel profiles usually have to be provided with special rust protection – also called corrosion protection – or fire protection for their use in steel construction or the steel trade.
For this purpose, Venjakob offers complete steel preservation lines that are precisely tailored to our customers’ needs. We handle all steps in the process.
In addition to our own experts for this product segment, we also draw on decades of experience provided by the employees of our U.S.-based subsidiary NUTRO Inc. They have developed numerous plate & shape lines and have earned an excellent reputation for it.
Complete steel preservation plants consist of:
- Individually coordinated conveyor systems
- A dust removal and cleaning unit
- Blasting equipment
- A coating system
- and subsequent post-drying
- Removal transport systems
Loading/feeding/conveyor systems
Both the feeding system for the preservation line and the conveyor system are individually adapted to your requirements.
For instance, cross transfers/cross transport systems are used in this context. Their advantage lies in their particular cost-effectiveness, as they manually collect workpieces to form batches for the coating process. This lets you save coating material and increases the throughput.
The transport through the entire coating system is automatically controlled in a continuous flow, with each conveyor system being, of course, tailored precisely to the customer’s requirements. Venjakob offers a wide range of handling and transport systems manufactured in-house.
Discharge / removal
Like the feeding system of the preservation line, the discharge can be freely configured. The transport technologies chosen are precisely tailored to the customer’s requirements. The workpieces can be removed by forklift or crane.
To avoid the production line coming to a stop if there are interruptions while unloading workpieces, the discharge and removal area can be designed flexibly, e.g. by using a cross transfer/cross conveyors that automatically transport to the left or right side of the discharge areas, or straight ahead, depending on how busy each area currently is.
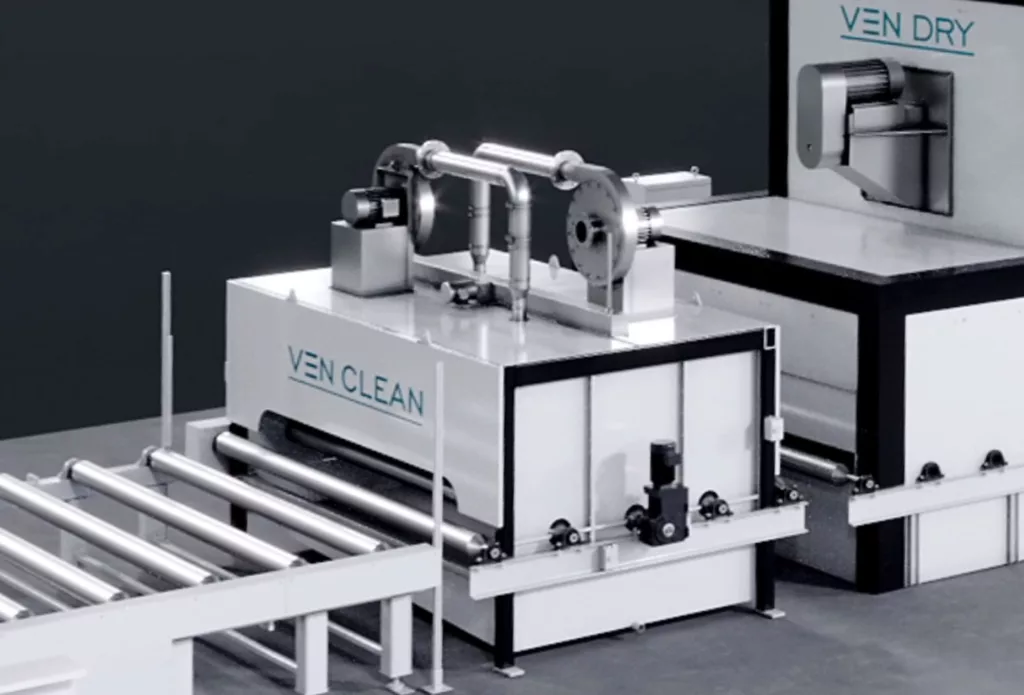
CLEANING AND DRYING, E.G. TO REMOVE CONTAMINATION FROM OUTDOOR STORAGE
Before the workpieces are coated, they must first be cleaned. Pre-cleaning also prevents dust, leaves water and dirt from being carried over into the subsequent processes.
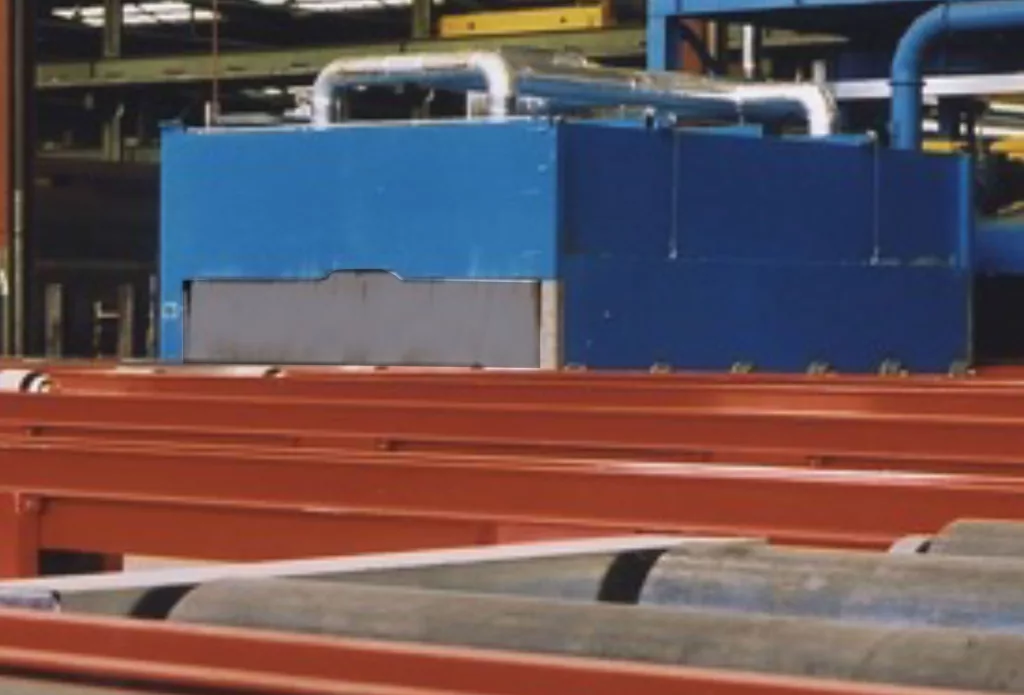
PRE-HEATING
Energy-efficient preheating is used to dry the workpieces and efficiently dry the coating material applied later.
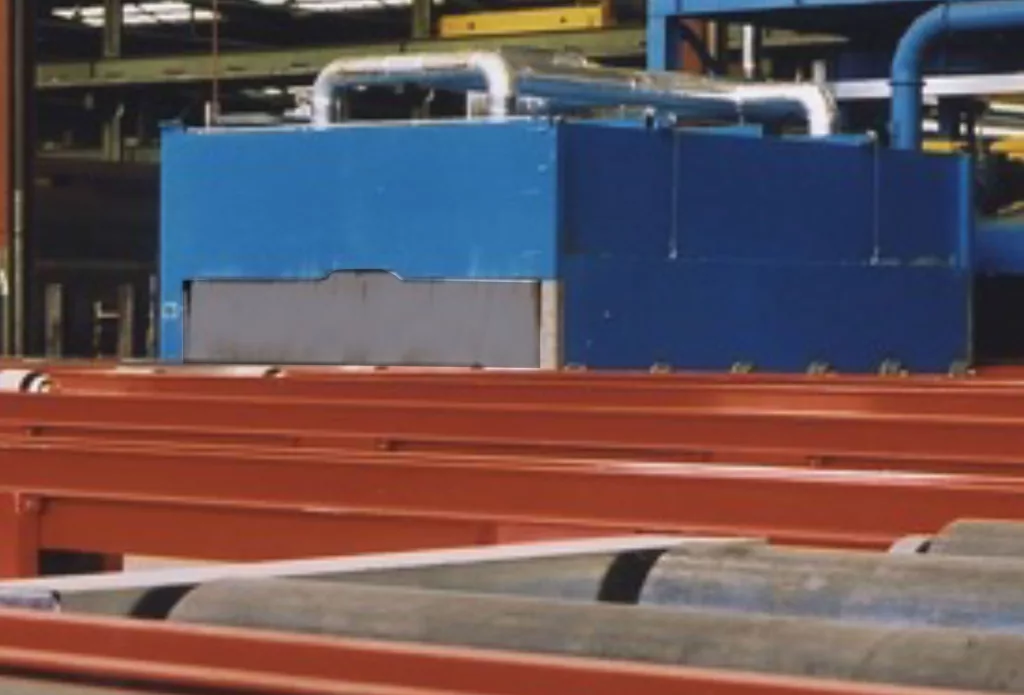
BLAST CLEANING SYSTEM BLAST CLEANING TO REMOVE LAYERS THAT IMPAIR QUALITY, SUCH AS RUST AND SCALE
In addition to degreasing , a suitable pre-treatment process is required to achieve a good feel and optimum corrosion protection.
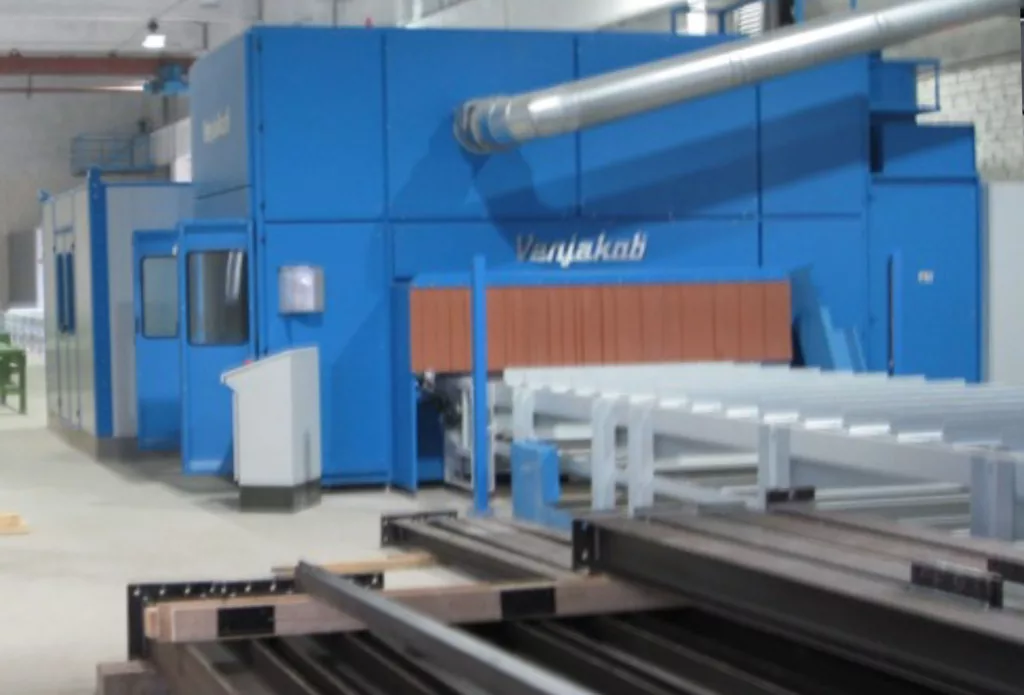
PAINTING
Von Venjakob and Nutro not only provide you with a coating system, but also a fully automated, coordinated coating process.
Accordingly, this is a complete line including pre-treatment and drying technology that operates in a continuous process.
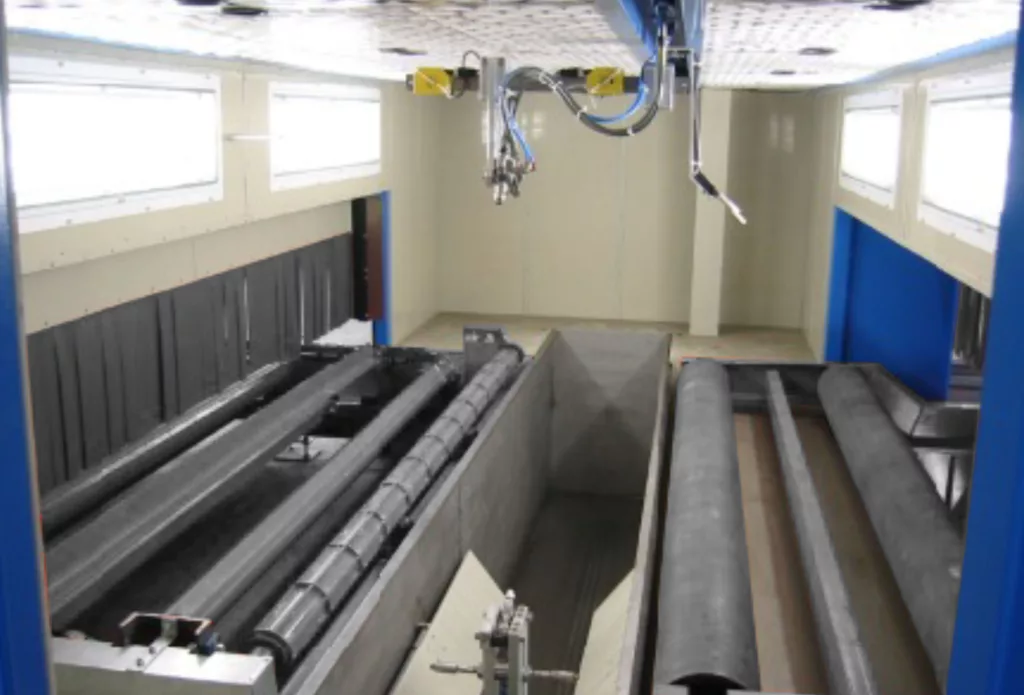
EFFICIENT HIGH PERFORMANCE COATING
Modern workpiece recognition systems are used to ensure the efficient and resource-saving paiting of many different parts.
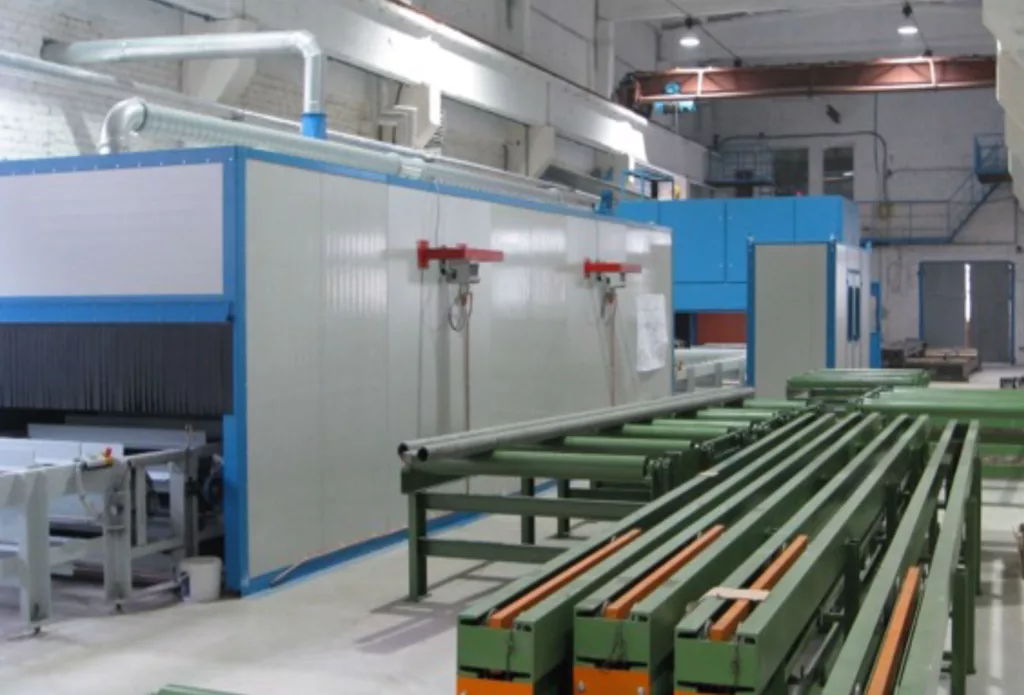
DRYING
Venjakob offers customized drying technology depending on the requirements.
To save energy, the warm exhaust air from the pre-dryer is fed into the paint dryer. Further energy is saved by operating the paint dryer in recirculation mode.
Discharge / Removal
Similar to the infeed of the preservation line, the outfeed can also be freely configured. The selected transport techniques are precisely tailored to customer requirements. The workpieces can be removed by forklift or crane.
To avoid a standstill if the workpiece removal should come to a standstill, the outfeed and removal area can be designed flexibly, e.g. by using an angled transfer/transverse transport system that conveys out on both sides and automatically supplies the left or right side for unloading, depending on the document status, or also conveys straight ahead.
Other advantages that make all the difference:
- Short assembly and commissioning times due to assembly of prefabricated modules on site incl. the option of a factory acceptance test
- Decades of cross-industry experience in the development and implementation of customer-specific coating and finishing solutions and in the integration of a wide variety of 2-component systems. Everything from a single source.
- Low space requirement due to extraction of the overspray in the spray booth on one side. This means that the system can be set up e.g. parallel to the building wall to save space (available up to a working width of 2000 mm (approx. 80 inches)
Workpiece detection:
Optionally available in two versions with the latest sensor technology for precise switching of the spray guns:
- in the spray booth, moving along on the spray gun carrier
- outside in front of the spray booth, independent of the spray gun carrier. Advantage: less contamination of the sensor technology
Digital features:
- Simplified process monitoring through real-time transmission of video images from the spray booth to the control station
- Digital transfer of process data and measured values to all common control systems
Efficient and resource-preserving:
- Pre-dryer: low energy consumption and optimum heat distribution due to innovative burner arrangement; precisely targets the workpiece. Operation with oil is also possible
- Low loss of coating material due to innovative arrangement of the mixing device in 2-component systems (short hose line)
- Highly homogeneous substrate coating and low material consumption,
- also optimal edge coating due to pull-and-push mode for the spray guns
- Brand-name airless spraying system with police filters for first-class coating results
Easy to clean:
- To further reduce the work required for cleaning, the coating system is protected by a film wrapping system in the bottom area. Optionally, a more environmentally friendly, lacquer-resistant paper band can be used in place of the film.
- Using a highly efficient extraction system with a brush separator, including a quick-change system for the brushes, reduces the cleaning and maintenance workload. An optional brush cleaning station can be added to further reduce maintenance work and filter consumption.
Long-term investment security through Venjakob plant technology
Venjakob's modular system also allows existing plants to be flexibly retrofitted and adapted to new conditions and requirements at a later date. You benefit from long-term planning and investment security as well as transparent pricing.
Your contact
Interested? Then let's talk! About the coating system to help you achieve your goals.