- Battery cell coating
CONTACT-FREE COATING OF BATTERY CELLS
Novel process: Coating replaces foiling of battery cells
Battery cells used in electric vehicles are usually covered with a protective film. A complex and costly process. Alternatively, there is now a special UV varnish that provides equally good protection for the sensitive cell modules.
Our engineers have developed a fully automated system solution for this new type of coating on behalf of the customer. Prismatic cell modules in various formats
can be coated without contact in a continuous process.
This has accelerated the entire battery cell production process and reduced costs.
Ultra-fine cleaning with plasma supports coating adhesion
Before coating, the battery cells are precision-cleaned to ensure perfect adhesion of the protective coating. Innovative open-air plasma technology is used for this purpose.
Compared to conventional cleaning methods, the process is significantly more environmentally friendly, selective and inline-capable. The surfaces of the battery cells are reliably cleaned of wafer-thin layers of dust and residual traces from the production process, e.g. oils or greases, so that the protective coating can be applied without gaps and long-term adhesion is achieved.
Contact-free coating process protects the battery cells
In the second step, the prismatic battery cells are coated with a special 100% UV protective coating in a fully automated, contact-free process.
Here, it is essential to protect the so-called terminals from overspray during the coating process. Venjakob developed a special workpiece carrier for the desired 6-sided coating in a single pass, which reliably protects the sensitive areas and electrical poles of the battery cell from overspray during the entire coating process.
In the spray booth, the cells are coated by permanently installed spray guns. As no gripping, turning or further handling is required, the risk of damage to the sensitive battery cells is minimized. The contact-free process also allows for increased production speed. To keep coating material consumption as low as possible, any excess coating that collects on the belt is removed and fed back into the process. After automatically passing through a UV curing tunnel and repeating these two steps in the continuous process, the coated cells are transported to the outfeed. Immediate curing means they can be processed directly. This speeds up the entire battery manufacturing process. The machine line processes battery cells in different formats without any changeover.
Innovative process achieves top results and reduces sources of error
The finely tuned process of ultra-fine cleaning and coating delivers outstanding results and minimizes sources of error in battery production.
The result is a highly effective and efficient alternative to expensive, time-consuming film wrapping, which has been highly appreciated by our client.
This is because the increased strength of the paint coating in contrast to film wrapping results in a further advantage for the battery module manufacturer: the battery cells can be bonded directly to the housing base while complying with all safety requirements. All safety-relevant aspects are taken into account.
TECHNICAL CHALLENGES, GOALS AND HIGHLIGHTS:
- Protection of the sensitive cell modules must be guaranteed
- No handling/turning/gripping -> no damage to the battery cells
- 6-sided coating of the battery cells in a continuous process
- Coating of different prismatic battery cell formats without retooling
- Immediate drying / curing of the coated cells -> enables immediate further processing
- Paint recovery -> reduced paint consumption
- Reliable all-round protection of the cell edges
- Increased production speed
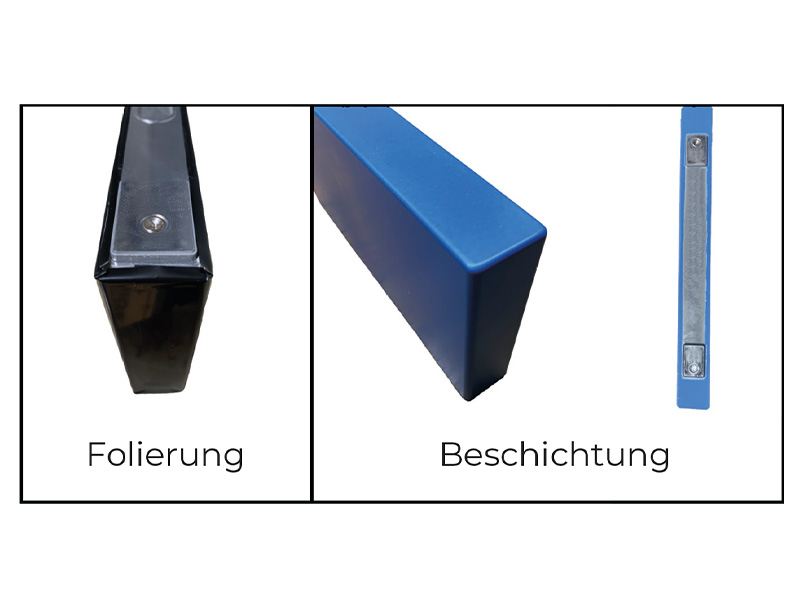
foiled and painted battery cell
The coating encloses and protects the sensitive battery cell more reliably than the film wrapping.

plasma treatment of a battery cell
Fine cleaning of a battery cell in a PTU (Plasma Treatment Unit) from Plasmatreat in preparation for the subsequent finishing with UV coating.
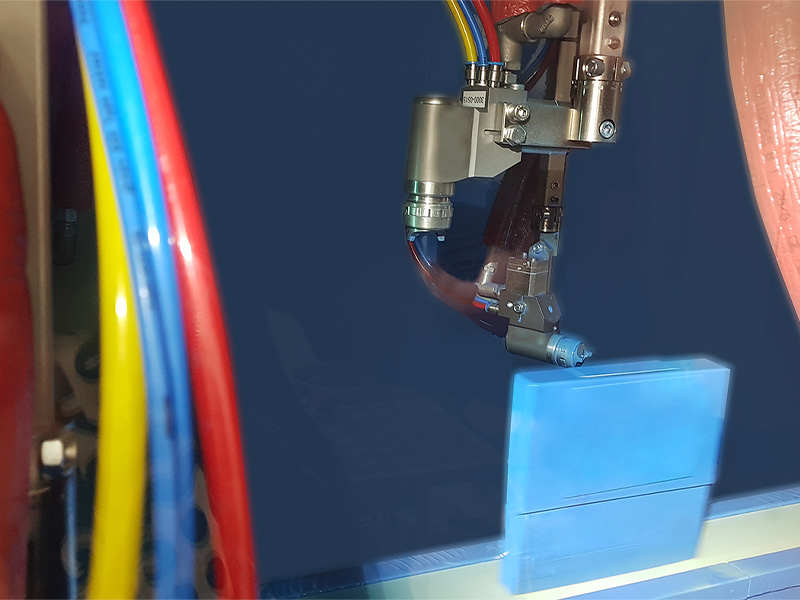
view into the venjakob spray coating booth
Contactless coating of different battery cell formats without changeover
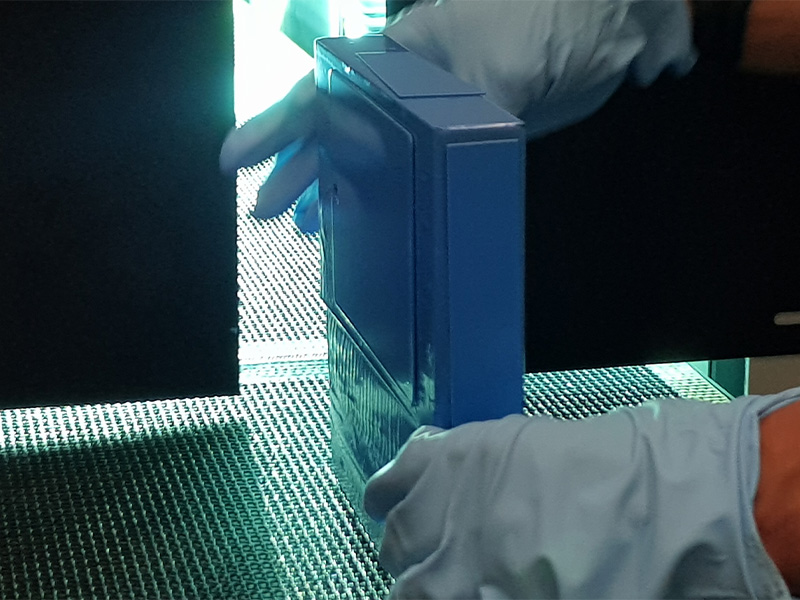
outlet from UV channel
Outlet of the battery cell coated and cured with 100% UV coating material, ready for the subsequent processing step
CONCLUSIONS:
The entire battery cell production process has been speeded up and costs further reduced thanks to the new coating process.
Have we piqued your interest? Would you like to find out more about our battery cell coating process or other finishing solutions?
Our team will be happy to advise you.
Your CONTACT PERSON
Interested? Let’s have a chat. About a special solution for whatever application – or generally about the system that benefits you in particular.
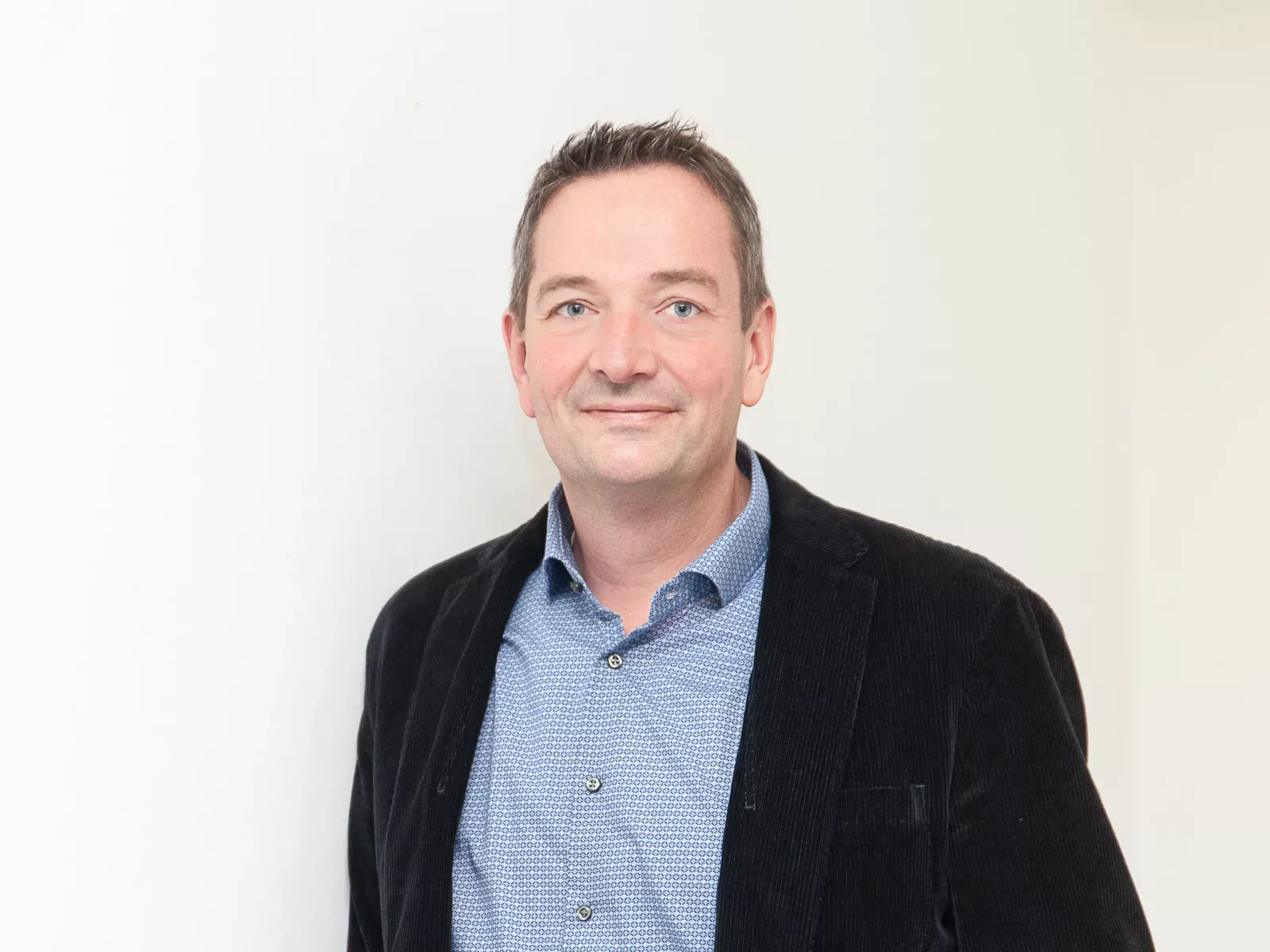
Gert Grosse Deters
General Industry|Automotive